In this fast-paced digital era, technology continues to evolve and transform various aspects of life, including how companies manage compliance reporting and workplace safety. One increasingly popular innovation is the use of digital logsheets. Digital logsheets are not merely a replacement for traditional paper logsheets but also an effective tool for enhancing compliance with regulations and safety standards. This article will discuss how digital logsheets function as a compliance reporting tool and their contribution to improving workplace safety.
1. Understanding Digital Logsheets
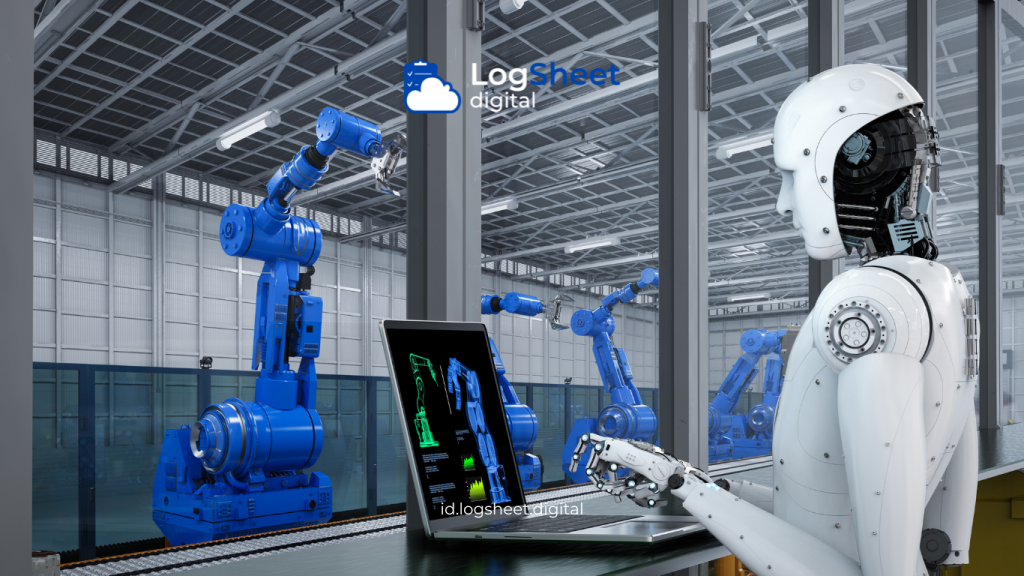
Read More: Digital Logsheets as a Step Towards Safety 4.0 in Industry
1.1. What is a Digital Logsheets?
A digital logsheets is an application or software used to record, manage, and analyze operational data digitally. This logsheets is typically accessed through devices such as tablets, smartphones, or computers, and allows users to input data in real-time. Compared to paper logsheets, digital logsheets offer various advantages, such as ease of access, faster data input, and the ability to analyze data more efficiently.
1.2. Differences Between Digital and Manual Logsheets
The primary difference between digital and manual logsheets lies in their storage media. Manual logsheets use paper and require physical recording, while digital logsheets allow for electronic recording and storage of data. This makes digital logsheets easier to access and manage and minimizes the risk of data loss due to physical document damage.
2. The Role of Digital Logsheets in Compliance Reporting
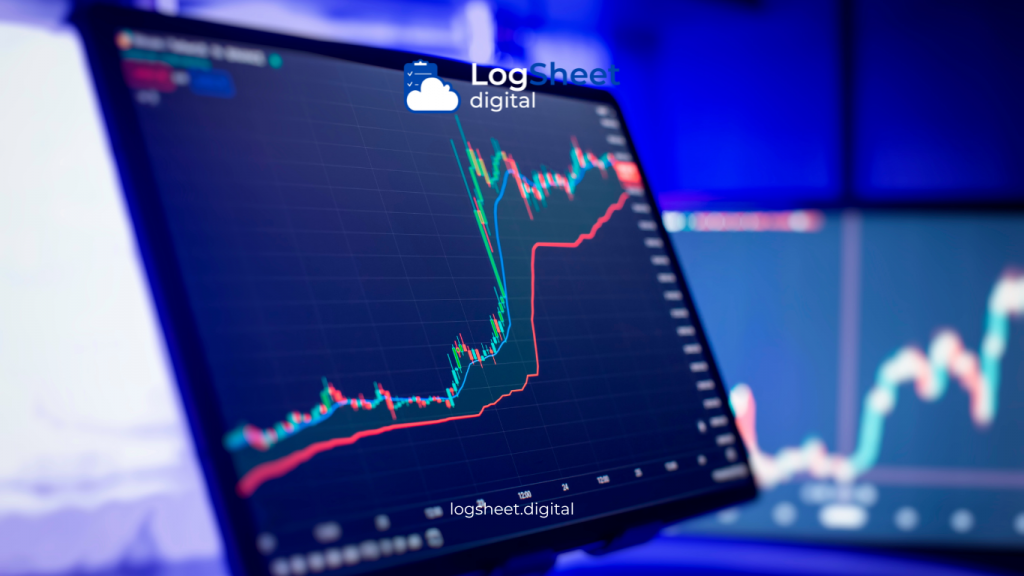
Read More: Efficiency in Accident Reporting: Digital Logsheets in Safety Equipment
2.1. Enhancing Data Accuracy and Reliability
In compliance reporting, data accuracy and reliability are crucial. Errors in recording can have severe consequences, especially when related to safety standards. Digital logsheets enable more accurate data input due to the automation and data validation features available within them. Users can enter data quickly, and the system automatically checks for errors or inconsistencies.
2.2. Accelerating the Reporting Process
Using digital logsheets speeds up the compliance reporting process because data can be accessed and sent in real-time. Managers and supervisors can monitor compliance with safety procedures without having to wait for time-consuming manual reports. Consequently, corrective actions can be taken immediately if violations or compliance issues are detected.
2.3. Facilitating Data Access and Storage
With digital logsheets, compliance reporting data can be stored in secure cloud or server environments, making it easier for authorized parties to access. This also reduces the risk of data loss that can occur with paper logsheets. Additionally, digitally stored data can be easily searched and retrieved if needed for audits or further examination.
3. Digital Logsheets as a Safety Improvement Tool
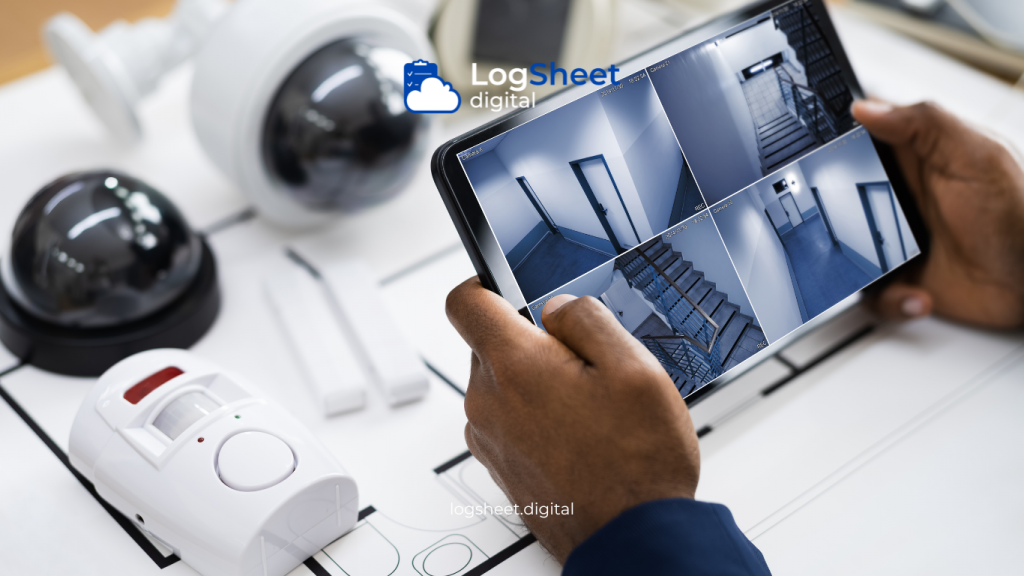
Read More: Successful Steps in Implementing Digital Logsheets in Safety Equipment
3.1. Monitoring Equipment Conditions in Real-Time
A critical aspect of workplace safety is ensuring that the equipment used in operations is always in good condition. Digital logsheets enable real-time monitoring of equipment conditions, so any damage or wear can be detected and repaired promptly before it poses a risk of accidents.
3.2. Enhancing Awareness and Compliance with Safety Procedures
Digital logsheets also play a role in increasing awareness and compliance with safety procedures. With automatic alert systems, employees can be reminded to perform checks or actions according to a predetermined schedule. This helps ensure that all safety procedures are carried out correctly and consistently.
3.3. Analyzing Data to Improve Safety Processes
Data collected through digital logsheets can be analyzed to identify trends or patterns that may indicate potential safety risks. For example, if data shows that a particular piece of equipment frequently experiences malfunctions, management can evaluate whether there are design or maintenance issues that need addressing. This data analysis also allows companies to continuously improve safety procedures based on findings from the data.
4. Implementing Digital Logsheets in the Workplace
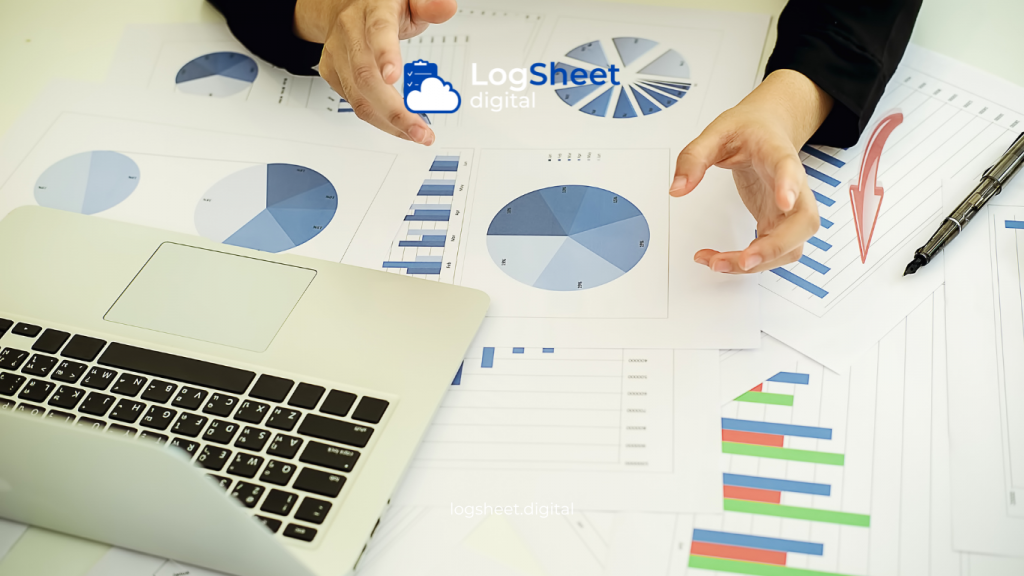
Read More: Enhancing Quality Oversight with Digital Logsheets: Workshop Industry Case
4.1. Implementation Steps
Implementing digital logsheets in the workplace requires careful planning. Key steps to take include:
- Evaluate Needs: Identify areas where digital logsheets will provide the greatest benefits, such as in compliance reporting and safety.
- Select a Platform: Choose digital logsheets software that aligns with operational needs and integrates easily with existing systems.
- Employee Training: Provide training to employees on how to use digital logsheets, including data entry and report access.
- Testing and Evaluation: Conduct initial testing to ensure the system operates correctly and perform periodic evaluations to identify areas for improvement.
4.2. Implementation Challenges
Implementing digital logsheets does not always proceed smoothly. Some challenges that may be encountered include:
- Resistance to Change: Employees accustomed to manual systems may find it difficult to adapt to new technology.
- Budget Constraints: The initial investment in hardware, software, and training can be a barrier, especially for small companies.
- Technical Issues: Digital systems are prone to technical problems such as network disruptions or software malfunctions, which can affect operations.
5. Case Study: Digital Logsheets Implementation in the Manufacturing Industry
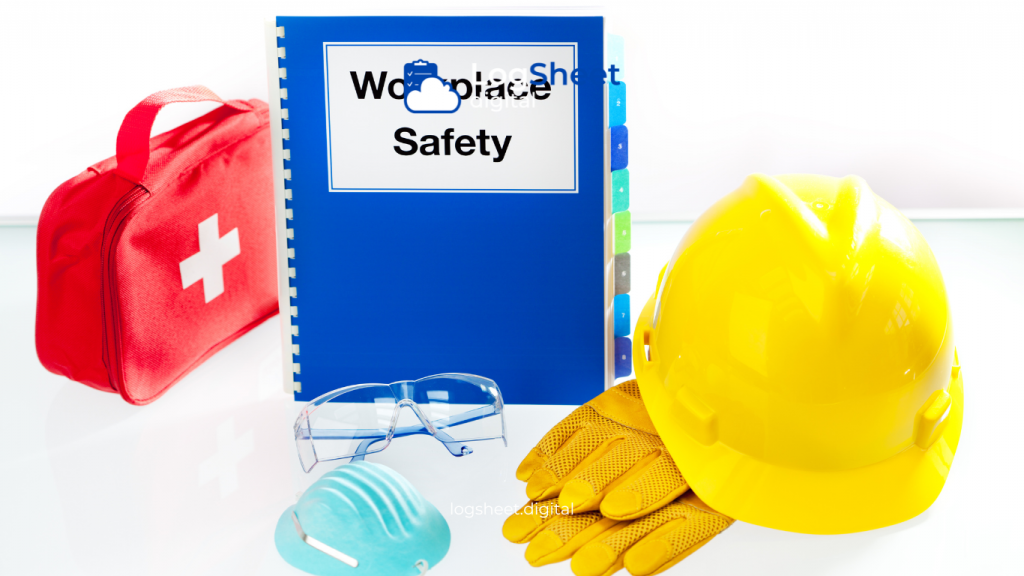
Read More: Improving Quality Control Accuracy with Digital Logsheets
5.1. Success of Implementation
A large manufacturing company successfully implemented digital logsheets for compliance and safety reporting. By using digital logsheets, the company reduced workplace accidents by 40% within the first year. This success was achieved through real-time monitoring of machine conditions and more in-depth data analysis, enabling timely preventive maintenance.
5.2. Learning from Challenges
Initially, the company faced resistance from employees accustomed to manual logsheets. However, through comprehensive training programs and involving employees in the change process, this resistance was overcome. Additionally, the company addressed technical issues by ensuring adequate IT support and routine system maintenance.
Conclusion
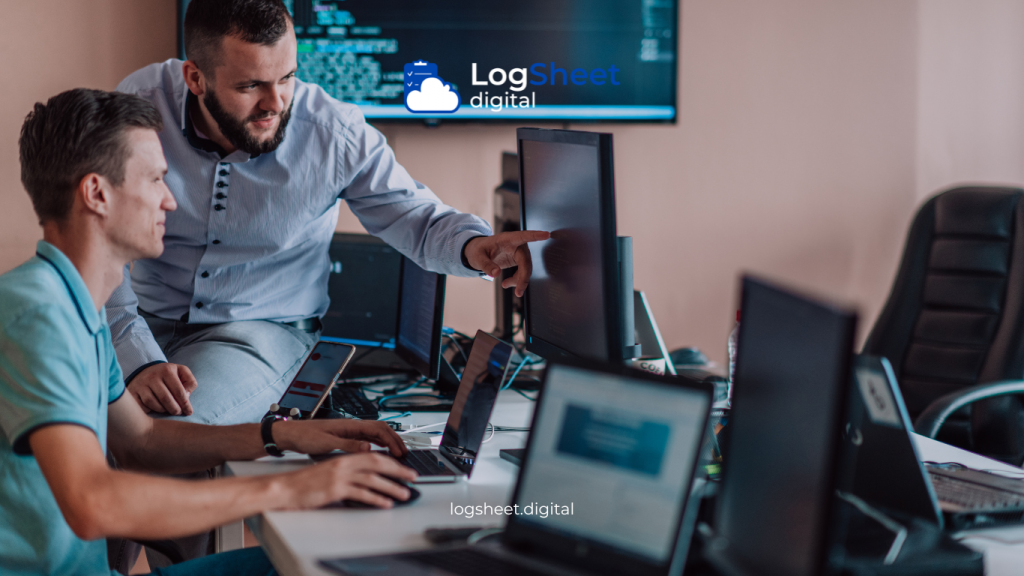
Read More: Steps to Successfully Implement Digital Logsheets for Safety Equipment
Digital logsheets have proven to be an effective tool for enhancing compliance reporting and safety in the workplace. With advantages in data accuracy, reporting speed, and in-depth analysis, digital logsheets help companies meet compliance standards and prevent workplace accidents. Although there are challenges in implementing them, the long-term benefits of digital logsheets far outweigh the difficulties, particularly in creating a safer and more efficient work environment. Therefore, companies aiming to improve compliance and safety should consider transitioning to digital logsheets as part of their safety management strategy.

comments (0)