In today’s digital era, technological transformation has become an unavoidable necessity for companies that want to remain competitive. One innovation that has had a significant impact on the manufacturing industry is the use of digital logsheets. By utilizing this technology, production plants around the world are beginning to optimize efficiency, reduce human error, and accelerate workflows. This article will explore in depth how digital logsheets are transforming work processes in production plants, the benefits gained, and the challenges that may be faced in their implementation.
What is a Digital Logsheet?
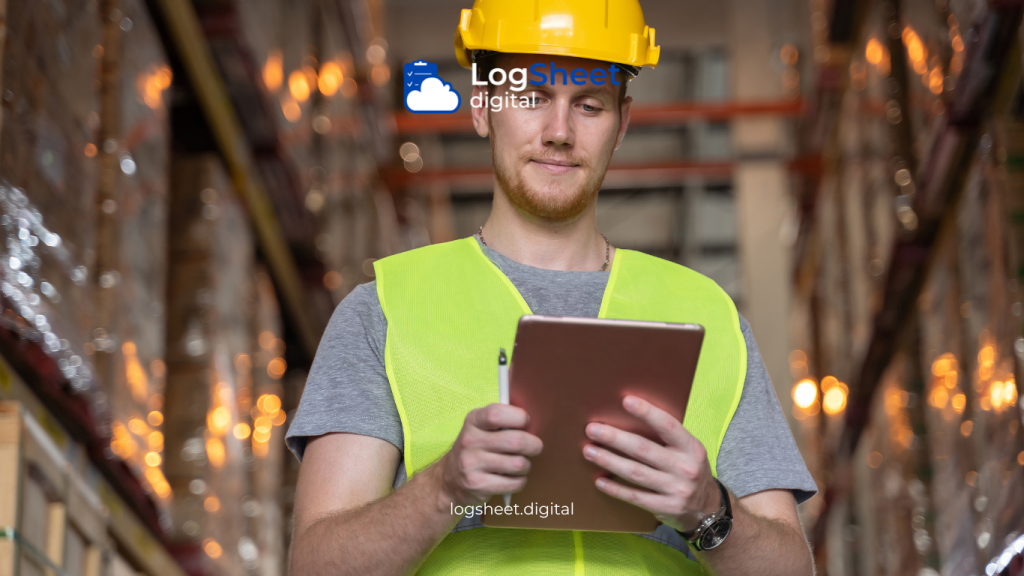
Read More: Real-Time Quality Monitoring: How Digital Logsheet is Changing Production
Digital logsheet is a replacement for manual logs typically used in production plants to record various operational data, such as equipment information, production activities, and routine inspections. Instead of using paper or spreadsheets, digital logsheet allows data to be recorded and accessed in real-time using digital devices such as tablets, computers, or smartphones.
With digital logsheet, the recorded data can be stored in a cloud-based system or internal storage integrated with other management software. This provides greater flexibility and reliability in monitoring and managing production processes.
Benefits of Digital Logsheet in Production Plants
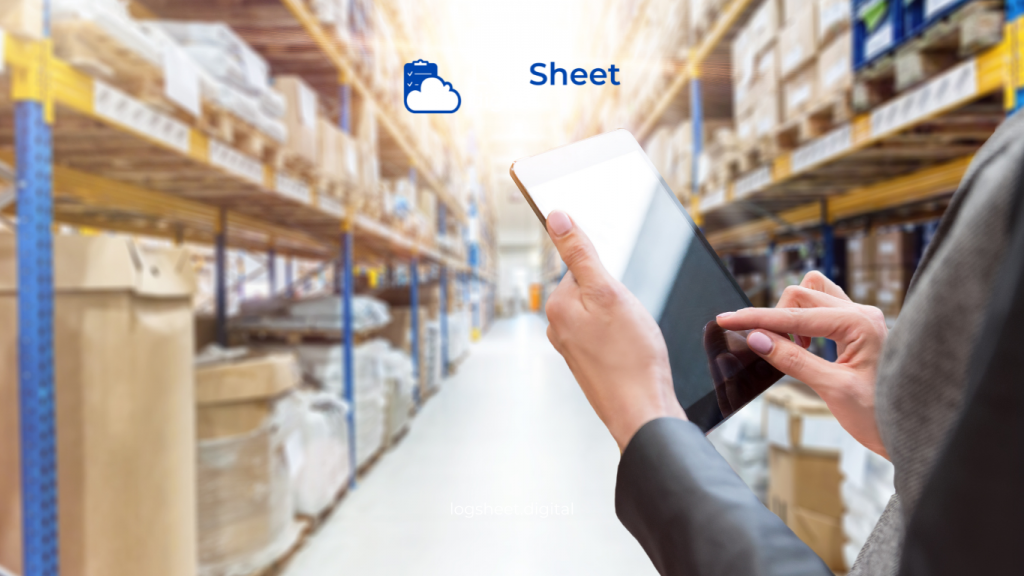
Read More: Data Analysis for Process Improvement: Benefits of Digital Logsheet in Production
The transformation to the use of digital logsheet in production plants offers several significant benefits, including:
1. Improving Operational Efficiency
One of the main benefits of digital logsheet is its ability to enhance operational efficiency. In production plants, time is a crucial factor. Every second lost due to manual recording, filing, and administrative errors can affect overall production output. With digital logsheet, recording is done automatically, and data can be updated in real-time, reducing the time needed for data collection and analysis.
2. Reducing Human Error
Manual recording by humans is highly susceptible to errors, whether due to negligence, imprecise measurements, or a lack of consistency in writing. Digital logsheet can reduce or even eliminate these errors because data input through digital devices is more structured and accurate. Additionally, companies can integrate this system with sensors or other automated devices to monitor machine conditions or production parameters directly, minimizing manual intervention.
3. Increased Data Security
In manual systems, companies usually store data in physical documents that are vulnerable to loss, damage, or manipulation. With digital logsheets, organizations can securely store data in cloud-based systems or internal servers protected by advanced security protocols. This ensures that critical information stays safe, remains accessible at any time, and is less likely to be lost.
4. Facilitating Decision-Making
With data available in real-time and presented in more understandable formats, plant management can make faster and more accurate decisions. For example, if there is an anomaly in production, such as a drop in machine performance or a spike in energy consumption, this issue can be quickly identified through digital logsheet. This allows management to take corrective actions before problems escalate.
5. Easing Collaboration
With digital logsheet, various departments within the plant, such as operations, maintenance, and management, can collaborate more easily. The same data can be accessed by multiple parties simultaneously, minimizing miscommunication and speeding up problem-solving processes. Better collaboration means increased productivity and fewer obstacles in workflow.
Positive Impact on Work Processes
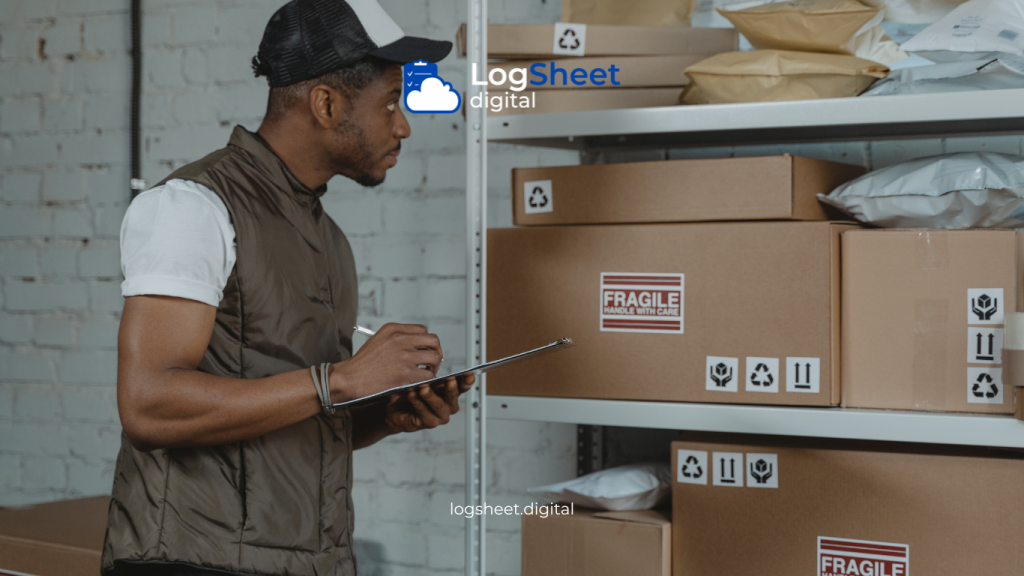
Read More: Exploring Production Potential: Advantages of Digital Logsheet in the Manufacturing Industry
The implementation of digital logsheet brings significant changes to various aspects of work processes in production plants. Here are several ways this technology transforms those processes:
1. More Effective Machine Performance Monitoring
In a plant environment, keeping machines operating optimally is very important. With digital logsheets, companies can monitor machine performance more systematically. They can analyze collected data, such as machine temperature, operational time, and energy consumption, to detect potential issues before major failures occur. This allows maintenance teams to take preventive actions, which is certainly more economical than repairing damages that have already occurred.
2. Optimizing Resource Usage
Production plants often need to manage various resources, such as raw materials, energy, and labor. With digital logsheets, companies can monitor and optimize the usage of these resources. For instance, they can analyze data on machine energy consumption to determine the best times to operate or shut down machines, making energy use more efficient.
3. Reducing Downtime
Production downtime is a significant issue often faced by plants. It can occur due to untimely maintenance or system failures. Digital logsheet allows maintenance teams to track when machines were last inspected or repaired and provides early warnings if maintenance is needed. This helps reduce unexpected downtime and ensures smooth production.
4. Improved Compliance with Standards and Regulations
Many manufacturing industries must comply with strict quality standards and regulations. Digital logsheet simplifies plants’ efforts to ensure that every step in the production process adheres to applicable regulations. Automatically storing historical data also facilitates auditing, as all necessary information remains organized and readily available.
Challenges in Implementing Digital Logsheet

Read More: Real-Time Quality Monitoring: The Role of Digital Logsheet in Production Control
Although digital logsheet offers many benefits, its implementation is not always without challenges. Here are some challenges that plants may face when adopting this technology:
1. High Initial Investment
One of the main barriers to adopting digital logsheet is the significant initial investment cost. Plants need to allocate funds to purchase hardware, software, and employee training. However, companies often offset these costs with the long-term benefits gained from increased efficiency and reduced operational costs.
2. Employee Adaptation
Technological transformation often faces resistance from employees who are comfortable with existing systems. Implementing digital logsheet requires training and education to ensure that all staff can use it effectively. Management must provide support and sufficient time for employees to adjust to the new technology.
3. Availability of Technological Infrastructure
To run digital logsheet optimally, plants need to have adequate technological infrastructure, such as stable internet networks and secure data storage devices. In some locations, especially plants situated in remote areas, this infrastructure may still pose a challenge.
Conclusion

Read More: Enhancing Production Transparency with Digital Logsheet: Case Study in the Food Industry
Digital logsheet is a crucial step in the transformation of work processes in production plants. This technology not only enhances operational efficiency and reduces human error but also provides better insights for decision-making, improves data security, and facilitates collaboration between departments. Although there are some challenges in its implementation, the long-term benefits of digital logsheet far outweigh the costs and efforts involved.
By transforming towards the digital era, plants that adopt digital logsheets will prepare themselves to face global competition, increase productivity, and ensure operational sustainability in the future. For the manufacturing industry, this innovation is no longer a choice but a necessity for survival and growth in the modern era.
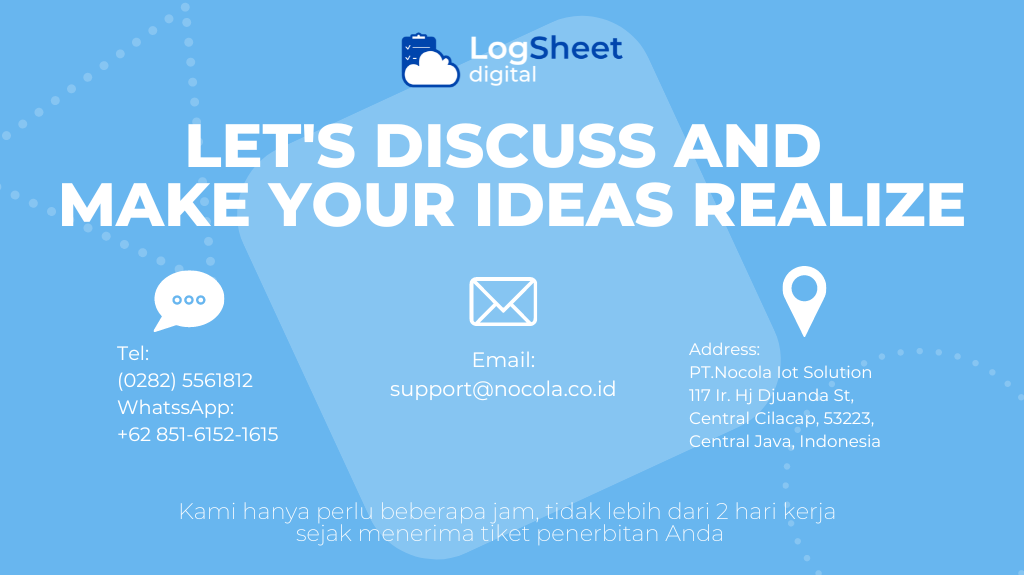
comments (0)