In the modern industry, safety is an aspect that cannot be overlooked. Workplace safety not only affects employee well-being but also has a direct impact on productivity and the company’s reputation. One key factor in ensuring optimal safety is the effective maintenance of safety equipment. Timely and regular maintenance can prevent unwanted accidents. In this digital era, digital log sheets are increasingly recognized as an effective tool to enhance maintenance effectiveness, ensuring higher safety in the workplace environment.
1. Maintenance and Safety: A Strong Connection
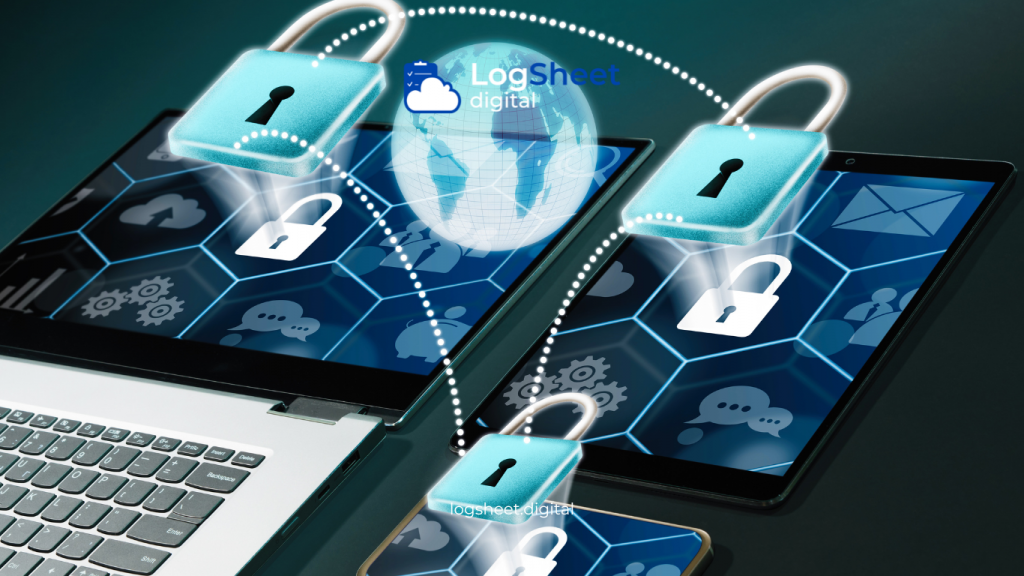
Read More: Implementing Digital Log Sheets in Safety Inspections
Maintaining safety equipment is a vital process to ensure that all tools and safety devices function properly when needed. Equipment such as fire extinguishers, gas detectors, personal protective equipment (PPE), and alarm systems must always be ready for use. If any of these tools fail to function during an emergency, the consequences can be fatal.
In many cases, inaccurate records, neglected maintenance schedules, and other human errors cause ineffective maintenance. Previously, teams recorded log sheets or maintenance records manually using notebooks or spreadsheets. However, these traditional methods have drawbacks, such as difficulties in tracking maintenance history, risks of data loss, and lack of visibility in decision-making.
2. What is a Digital Logsheet?

Read More: Sustainability in Safety: How Digital Log Sheets Impact the Industry
A digital logsheet is a maintenance recording system that uses digital technology to replace manual recording methods. Digital logsheets allow safety managers and maintenance technicians to record, track, and manage maintenance activities in real-time through a digital platform.
This system facilitates scheduling maintenance, ensures the availability of tools, and allows for more effective monitoring of equipment performance. With a digital log sheet, users can clearly record every maintenance activity and monitor the status of safety equipment anytime and anywhere.
3. Advantages of Digital Logsheets in Safety Maintenance

Read More: Digital Log Sheets as a Compliance Reporting and Safety Improvement Tool
3.1. Real-Time Recording
One of the main advantages of digital log sheets is the ability to record in real-time. Each time maintenance is performed, the data is immediately saved in the system. This reduces the risk of errors or omissions in recording and ensures that information is always up to date.
3.2. Automated Maintenance Reminders
Digital log sheets have automatic reminder features that notify the maintenance team when the next maintenance is due. This feature is very useful for maintaining compliance with maintenance schedules, which people often overlook when managing it manually. Automated reminders help teams ensure that every tool gets inspected regularly and meets safety standards.
3.3. Secure and Organized Data Storage
Digital log sheet systems offer more secure and structured data storage compared to manual records. The maintenance history of each piece of equipment can be easily and quickly accessed. Additionally, digitally stored data has a lower risk of damage or loss, unlike physical records that can be lost, burned, or damaged.
3.4. Safety Equipment Performance Analysis
Digital log sheets also provide the ability to analyze safety equipment performance over time. By monitoring stored maintenance data, managers can identify patterns of failures or recurring issues and determine whether a piece of equipment needs to be replaced or just repaired.
3.5. Accessibility and Mobility
Digital log sheet systems are typically cloud-based, allowing data access from various devices such as laptops, tablets, or phones. This enables maintenance teams and safety managers to monitor and manage maintenance from anywhere, without being physically present at the work site.
4. Implementing Digital Logsheets in Safety Systems

Read More: Digital Log Sheets: A Revolution in Safety Equipment Monitoring and Maintenance
4.1. Determining Equipment Needs and Specifications
The first step in implementing digital log sheets is to determine the specific needs of the company. Each industry has different safety requirements, so it is important to choose a digital log sheet solution that suits the types of equipment and maintenance processes in place. The system must be capable of handling various types of safety equipment and meet applicable safety regulation standards.
4.2. User Training
One of the challenges in adopting new technology is ensuring that the entire team understands how to use it. Training for technicians and maintenance managers is essential so they can make the most of the digital log sheet features. This training includes how to record maintenance activities, how to utilize automatic reminders, and how to analyze stored maintenance data.
4.3. Integration with Other Systems
To maximize the effectiveness of digital log sheets, integrate the system with other management platforms, such as asset management systems or ERP (Enterprise Resource Planning) systems. This integration allows companies to gain broader visibility into their entire operations, including safety equipment, maintenance performance, and inventory management.
5. Enhancing Safety through Digital Logsheets

Read More: APAR (Light Fire Extinguisher): Its Importance in Environmental Safety
The use of digital log sheets can significantly enhance workplace safety. With this system, the potential for accidents due to damaged or poorly maintained equipment can be minimized. Additionally, digital log sheets ensure compliance with applicable safety regulations, ultimately protecting the company from legal sanctions or lawsuits due to negligence.
5.1. Reducing Equipment Failure Risks
Well-scheduled routine maintenance through digital log sheets helps reduce the risk of safety equipment failure. Technicians can quickly identify equipment that requires repair or replacement before more serious issues arise.
5.2. Improving Compliance with Safety Regulations
In many industries, companies are required to comply with strict safety regulations. Digital log sheets make it easier for companies to record and report every maintenance activity to the relevant authorities, as well as provide evidence of compliance when needed.
5.3. Operational Efficiency
With digital log sheets, the maintenance process becomes more efficient. Managers can easily monitor when and who performed the last maintenance, as well as which tools need to be checked immediately. This efficiency not only improves safety but also reduces operational costs that may arise from equipment failure.
6. Challenges in Implementing Digital Logsheets

Read More: Efficiency of Safety Equipment through Digital Log Sheets
Despite its many benefits, implementing digital log sheets also comes with some challenges. One of them is the initial cost required to adopt this technology. Additionally, resistance from employees towards system changes can also be an obstacle during the implementation phase.
However, with the right approach, such as providing adequate training and demonstrating the long-term benefits of this system, you can overcome these challenges.
7. Conclusion
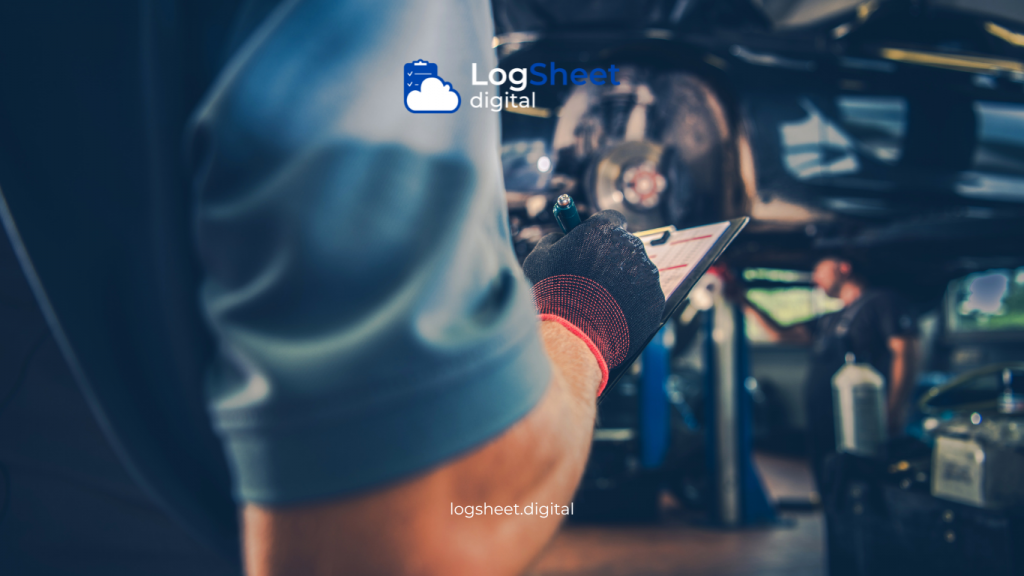
Read More: Digital Log Sheets: Enhancing Safety in Industry
The implementation of digital log sheets in the maintenance of safety equipment offers various advantages that can enhance operational effectiveness and efficiency. From real-time recording, automated reminders, to performance analysis of equipment, digital log sheets help companies ensure that every piece of safety equipment functions properly and meets standards.
Ultimately, digital log sheets not only enhance maintenance effectiveness but also minimize the risk of workplace accidents, ensure compliance with safety regulations, and reduce costs that may arise from damage or equipment failure. By adopting digital log sheet solutions, companies can create a safer and more efficient work environment.
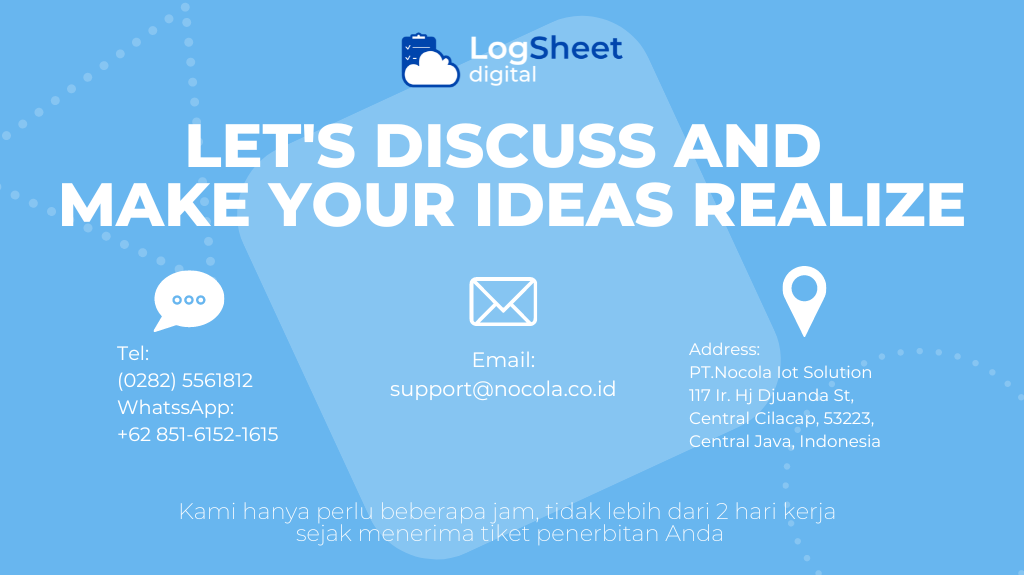
leave your comments