In the world of automotive workshops, time management is the key to maintaining efficient operations. When vehicles or machines require repairs, excessive downtime can harm both customers and the workshop itself. For example, every hour wasted due to maintenance delays or shortages of spare parts can add to operational costs and diminish customer trust. The Digital Logsheet for Downtime Reduction presents a solution to tackle this issue. By implementing an efficient digital logsheet system, workshops can manage wait times better, minimize downtime, and ensure that the repair processes run smoothly.
What is a Digital Logsheet?

Read More: Digital Logsheet and Sustainability: Optimizing Workshop Resource Usage
A digital logsheet is a technology-based system used to record and manage maintenance, repair, and operational activities in a workshop electronically. Unlike manual recording using paper, a digital logsheet allows data to be recorded automatically through digital devices such as tablets or computers. All this information is stored in a system that can be accessed in real-time by technicians, managers, and other authorized parties.
In the context of a workshop, the digital logsheet functions to record the repair history of vehicles, routine maintenance, spare part usage, and working time. With integrated data, workshops can reduce wait times between each repair process and enhance overall efficiency.
Challenges of Wait Times and Downtime in Workshops

Read More: Digital Logsheet in Improving Workshop Performance and Cost Reduction
Before discussing the effectiveness of digital log sheets further, it is essential to understand the challenges faced by workshops regarding wait times and downtime.
1. Lack of Real-Time Information
One of the primary causes of long wait times in workshops is the lack of real-time information about the condition of vehicles being repaired or the status of spare parts. Manual recording often makes it difficult for technicians or workshop managers to know the latest status of a repair.
2. Inefficient Spare Part Management
Spare parts that are not available on time or are poorly identified become a major cause of long downtime. When the necessary spare parts for repairs are unavailable, technicians must wait until the items arrive, resulting in prolonged downtime and delayed repair processes.
3. Mistakes in Maintenance Scheduling
Improperly timed or poorly coordinated maintenance scheduling can also prolong wait times. Missed or delayed routine maintenance can potentially lead to more significant damage, requiring longer repair times.
4. Difficulty in Tracking Repair History
Without well-organized records, technicians often struggle to track the repair history of a vehicle. This makes the diagnosis process longer and less efficient, ultimately extending wait times.
Advantages of Digital Logsheet in Reducing Wait Times and Downtime

Read More: Overcoming Implementation Challenges of Digital Logsheet in the Workshop Industry
Implementing a digital logsheet in workshops offers various advantages that directly impact the reduction of wait times and downtime. Here are some key benefits of digital log sheets:
1. Real-Time Information and Data Transparency
One of the main advantages of digital log sheets is their ability to provide information in real-time. All workshop activities, from vehicle intake to repair status, can be monitored through the digital logsheet system. Technicians and workshop managers can know instantly which vehicles are being repaired, the spare parts on order, and estimated completion times.
With this transparency, communication among teams in the workshop becomes more efficient. Each technician can access the information they need without waiting, significantly reducing wait times.
2. More Efficient Spare Part Management
Digital log sheets enable workshops to track spare part usage more accurately. When technicians record spare part usage through the digital system, workshop managers can see available stock and order necessary parts before running out.
Additionally, the digital logsheet system can be integrated with inventory management systems, making stock management more efficient. With good management, downtime caused by spare part shortages can be minimized.
3. Better Maintenance Scheduling
Digital log sheets allow workshops to plan routine vehicle maintenance more regularly. This system automatically sends reminders when a vehicle requires maintenance, enabling technicians to schedule maintenance at the right times.
Timely maintenance can prevent significant damage that leads to long downtimes. Furthermore, with good scheduling, workshops can avoid job backlogs that could extend wait times.
4. Improving Diagnostic Accuracy
With digital log sheets, technicians can quickly and easily access vehicle repair history. This information helps technicians diagnose issues more accurately and avoid time-consuming trial-and-error processes. Better diagnostic accuracy contributes to faster repairs, thereby reducing wait times and downtime.
5. Data-Driven Decision Making
Data stored in digital log sheets enables workshops to analyze their performance and make decisions based on accurate information. For instance, workshops can identify patterns of damage in certain vehicles and decide to perform maintenance more frequently on those vehicle types.
Data-driven decision-making helps workshops plan operations better, ultimately impacting the reduction of wait times and downtime.
Case Study: Implementation of Digital Logsheet in an Automotive Workshop
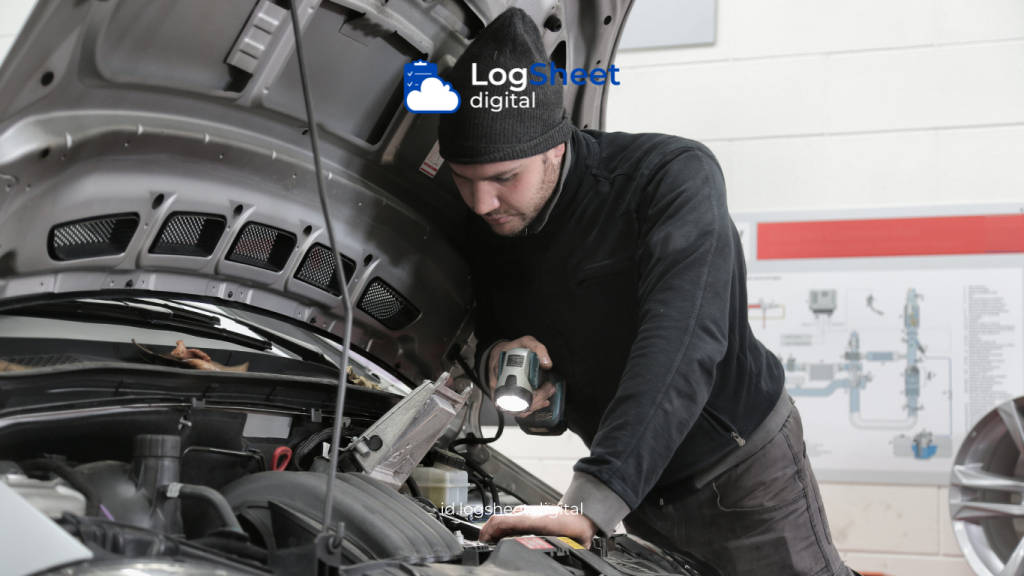
Read More: Enhancing Quality Oversight with Digital Logsheet: Workshop Industry Case
An automotive workshop in Jakarta that adopted a digital logsheet successfully reduced downtime by 25% in the first year of implementation. Before using the digital logsheet, the workshop frequently experienced repair delays due to difficulties in tracking spare parts and vehicle repair histories.
After implementing the digital logsheet, all data related to vehicle repairs was stored in a centralized system. Technicians could access this information in real-time and know the status of necessary spare parts. Spare part stock management also became more efficient, with automatic reminders when stock approached minimum levels.
Furthermore, the digital logsheet helped the workshop plan routine maintenance for customer vehicles more effectively. Customers received notifications via email or SMS when their vehicles required maintenance, thus reducing downtime caused by sudden breakdowns.
Challenges in Implementing Digital Logsheet

Read More: Digital Logsheet for Deeper Data Analysis and Decision Making
Although digital log sheets offer many benefits, their implementation does not always go smoothly. Here are some common challenges faced by workshops in adopting digital log sheets:
1. Resistance to Change
One of the main challenges in implementing digital log sheets is resistance to change. Many technicians accustomed to manual recording methods may find it difficult to adapt to the new system. To address this, workshops need to provide adequate training so all users can effectively use the digital logsheet system.
2. Implementation Costs
Although digital log sheets can save operational costs in the long run, initial implementation costs may be a barrier for some workshops. Workshops need to invest in hardware, software, and employee training.
3. Technology Infrastructure
Inadequate technology infrastructure, such as unstable internet connections or outdated devices, can hinder the optimal use of digital log sheets. Workshops need to ensure they have the necessary infrastructure to support smooth operation of the system.
Successful Steps in Implementing Digital Logsheet
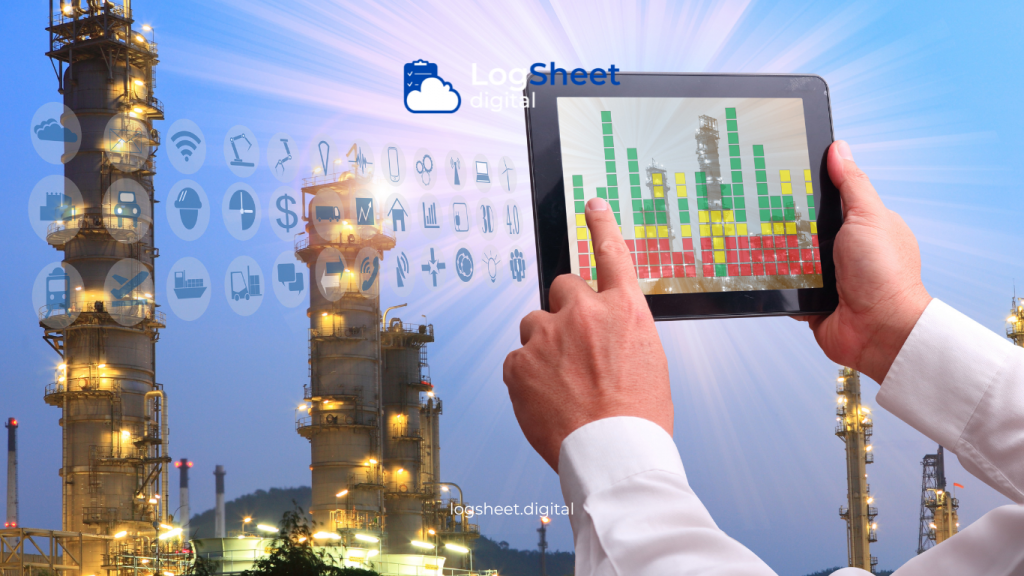
Read More: Digital Logsheet and Calibration Performance Analysis: Measurement and Improvement
To overcome the above challenges and ensure successful implementation of digital log sheets, workshops need to take the following steps:
1. Training and Education
Providing training for technicians and other staff is a key step in implementing digital log sheets. They need to understand how to effectively use the system, as well as the benefits that will arise from adopting this technology.
2. Evaluate Workshop Needs
Before adopting digital log sheets, workshops need to evaluate their operational needs. This includes determining the types of devices needed, data storage capacity, and features relevant to workshop activities.
3. Integration with Other Systems
To optimize the use of digital log sheets, workshops need to integrate this system with other management systems, such as inventory management or spare part ordering management.
Conclusion
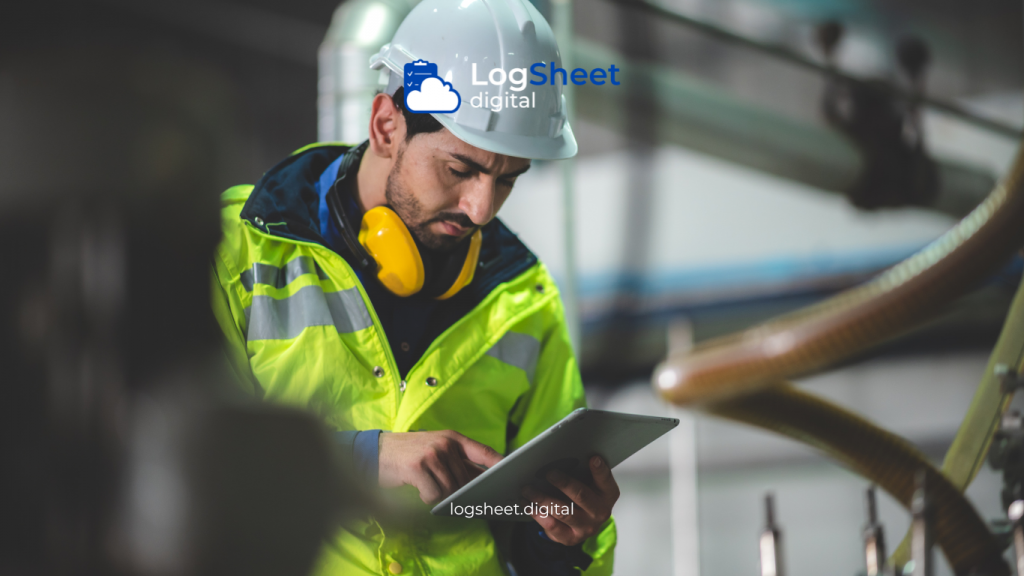
Read More: Towards Industry 4.0: Transforming Industries with Digital Logsheet
Digital log sheets have proven effective in reducing wait times and downtime in workshops. With information accessible in real-time
, efficient spare part management, and improved maintenance scheduling, workshops can operate more efficiently and provide better service to their customers.
However, successful implementation requires a comprehensive understanding of the challenges faced and appropriate strategies to overcome them. By prioritizing training, evaluating needs, and integrating with existing systems, workshops can maximize the benefits of digital log sheets and create a more productive work environment.
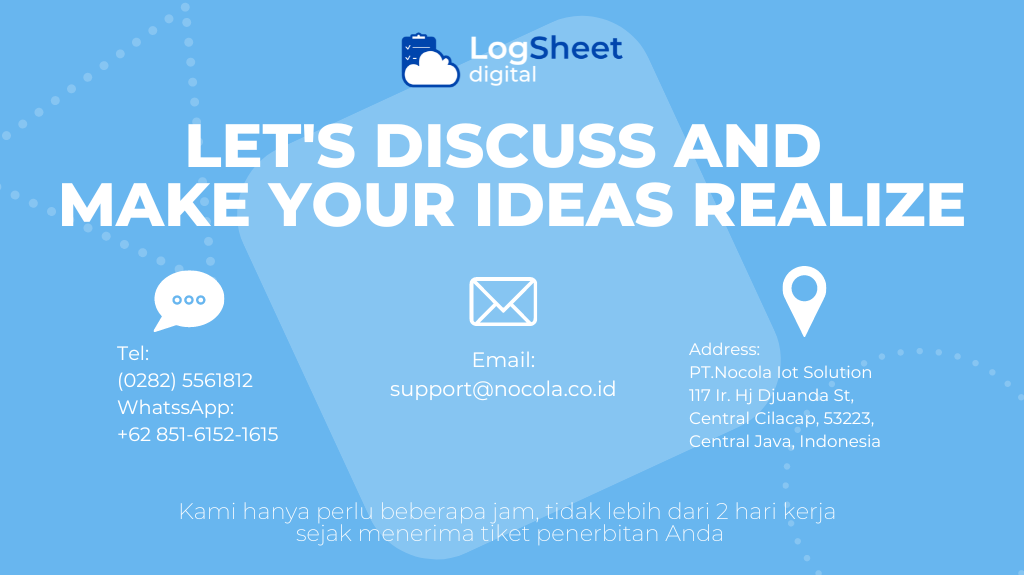
leave your comments