The development of digital technology has brought significant changes across various industries, including safety equipment management. Digital logsheets are an important innovation aimed at replacing manual recording with a more efficient and accurate system. However, despite the clear benefits, the implementation of digital logsheets for safety equipment is not without challenges. This article will discuss these challenges and provide solutions to overcome them.
1. The Importance of Safety Equipment in Industry

Read More: Effectiveness of Higher Maintenance: Digital Logsheets in Safety
Safety equipment plays a crucial role in protecting workers and company assets from workplace accidents. With the increasing complexity of industrial processes, the need for regular monitoring and maintenance of safety equipment becomes very important. Any failure or damage to safety equipment can have fatal consequences, both in terms of health and operational efficiency. Therefore, accurate and consistent record-keeping is essential.
2. What is a Digital Logsheets?

Read More: Implementing Digital Logsheets in Safety Inspections
Digital logsheets are electronic recording systems that replace traditional paper formats in documentation processes. In safety equipment management, digital logsheets are used to record inspections, maintenance, calibration, and monitoring of equipment conditions. This system utilizes cloud-based technology, IoT (Internet of Things), and software to ensure that all data is stored securely, easily accessible, and integrated with other management systems.
2.1 Benefits of Digital Logsheets for Safety Equipment
Using digital logsheets has several advantages over traditional methods, such as:
- Time Efficiency: Recording and accessing data becomes faster and does not require physical checks at locations.
- Data Accuracy: Reduces the risk of human error in manual recording.
- Transparency: Digitally stored data can be easily audited and accessed by relevant parties at any time.
- Better Management: Provides automatic alerts for equipment that needs inspection or servicing, reducing potential accident risks due to neglected equipment.
3. Challenges in Implementing Digital Logsheets
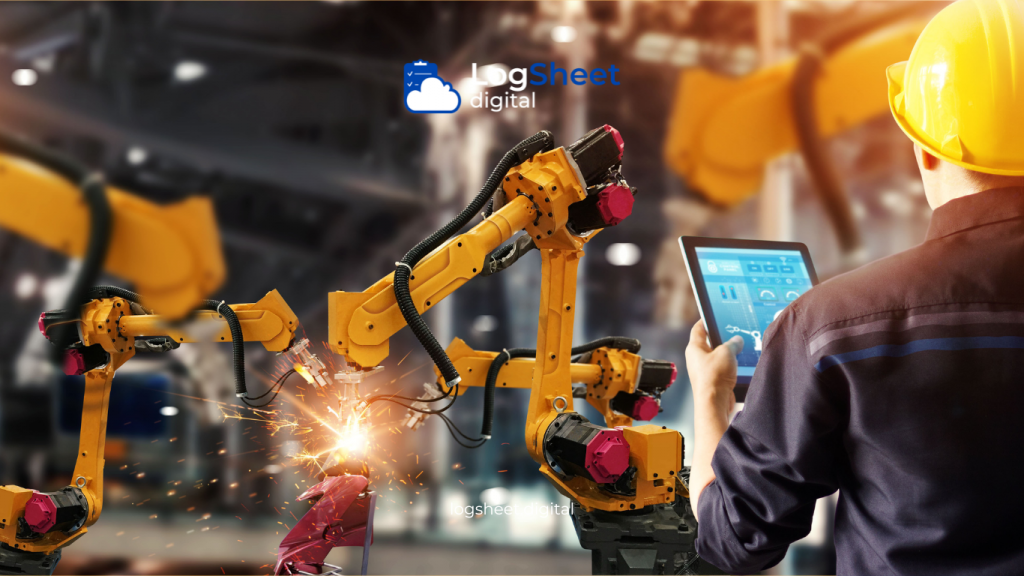
Read More: Sustainability in Safety: How Digital Logsheets Affect the Industry
Despite the many advantages of digital logsheets, their implementation does not always go smoothly. Several challenges need to be addressed by companies, particularly regarding the application to crucial safety equipment.
3.1 Lack of Awareness and Understanding of Technology
One major challenge is the lack of awareness and understanding of the benefits and workings of digital logsheets. Many companies are still hesitant to switch from manual systems due to familiarity with old methods or concerns about difficulties adapting to new technology.
Solutions:
- Training and Education: Companies need to provide comprehensive training for employees on how to use digital logsheets and how this technology can enhance safety and work efficiency.
- Communicating Benefits: Clearly explain how digital logsheets can simplify recording, monitoring, and maintaining safety equipment.
3.2 Implementation Costs
The initial costs of implementing digital logsheets can be a barrier, especially for small or medium-sized enterprises. The system requires investments in hardware, software, and training.
Solutions:
- Thorough Budget Planning: Companies should create long-term budget plans that consider the return on investment (ROI) from implementing digital logsheets.
- Phased Approach: Implementation can be carried out in phases, starting with the most critical parts of the company’s safety system before broader application.
3.3 Limitations of Technological Infrastructure
Implementing digital logsheets requires adequate technological infrastructure, such as stable internet connections and supporting hardware. In some areas, especially remote industrial locations, this infrastructure may not be available or adequate.
Solutions:
- Collaboration with Technology Providers: Companies can partner with technology service providers to develop the necessary infrastructure.
- Utilization of Offline Systems: Some digital logsheets providers offer solutions that can function offline and synchronize data when internet connectivity is restored.
3.4 Resistance to Change
The transition from manual systems to digital ones often meets resistance from employees who are accustomed to old methods. They may feel uncomfortable or worried about their ability to operate the new system effectively.
Solutions:
- Participatory Approach: Involve employees from the beginning of the implementation process, seeking input and demonstrating how digital logsheets can assist them in their work.
- Ongoing Training: Provide continuous training to help employees feel more confident and familiar with the new system.
3.5 Data Security
Data security is a primary concern in the implementation of digital logsheets, especially those based in the cloud. If not properly protected, data could be vulnerable to theft or manipulation, potentially jeopardizing company operations and workplace safety.
Solutions:
- Strong Security Systems: Ensure that the digital logsheet system includes data encryption, multi-factor authentication, and firewall protection.
- Regular Audits: Conduct regular security audits to identify and address potential vulnerabilities in the system.
4. Successful Strategies for Implementing Digital Logsheets
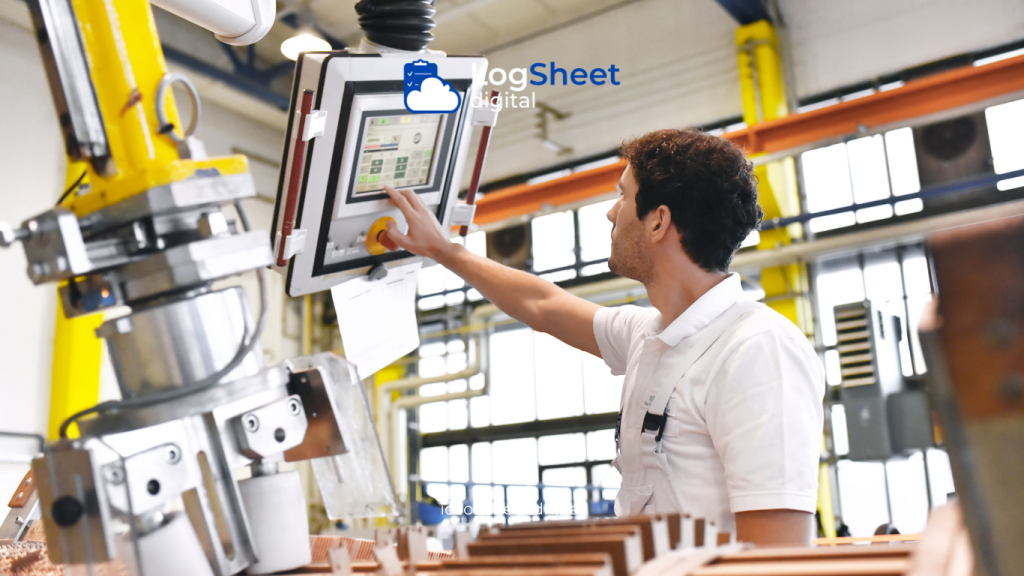
Read More: Digital Logsheets as Compliance Reporting Tools and Safety Enhancements
To overcome these challenges, companies can adopt several strategies to ensure the successful implementation of digital logsheets for safety equipment.
4.1 Identifying the Company’s Specific Needs
Every company has different needs regarding safety equipment management. Before implementing digital logsheets, it’s essential to identify specific requirements that align with the company’s operations.
4.2 Choosing the Right Service Provider
Selecting the right digital logsheets provider is crucial. Companies should choose a provider with a strong track record, offering features that meet their needs and capable of providing adequate technical support.
4.3 Integrating with Other Systems
The implemented digital logsheet system should be able to integrate with existing management systems, such as Computerized Maintenance Management Systems (CMMS) or Environmental, Health, and Safety (EHS) management systems. This integration will facilitate data management processes and improve operational efficiency.
4.4 Regular Monitoring and Evaluation
After the digital logsheets are implemented, it’s important to conduct regular monitoring and evaluation of the system’s effectiveness. This includes assessing performance, data reliability, and employee acceptance of the new system.
5. Positive Impact of Digital Logsheets on Workplace Safety
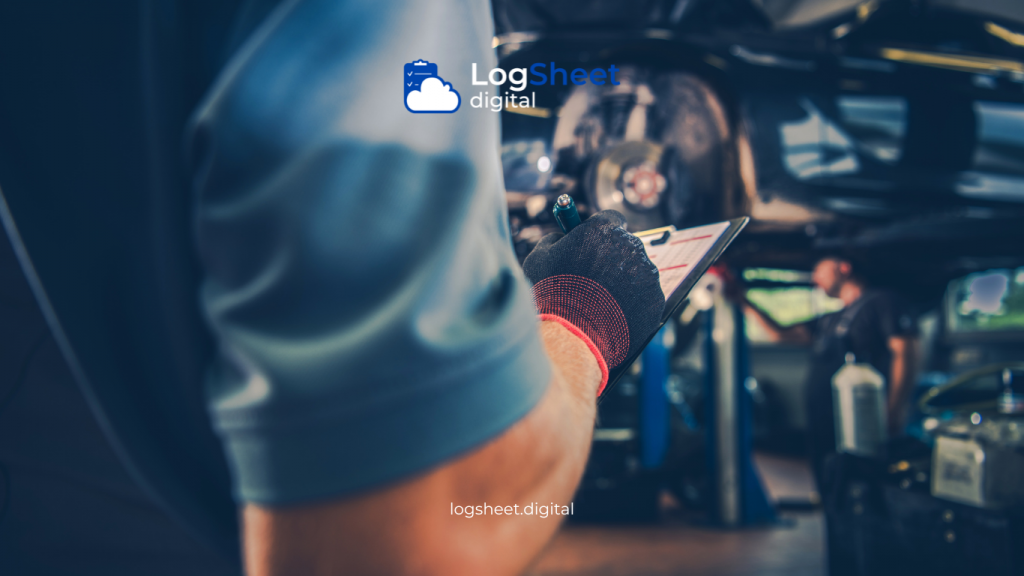
Read More: Efficiency in Accident Reporting: Digital Logsheets in Safety Equipment
A successful implementation of digital logsheets will have a positive impact on workplace safety within companies. With more accurate record-keeping and real-time monitoring, the potential for workplace accidents can be minimized. Additionally, operational efficiency will increase, as maintenance and inspection processes for equipment can be carried out more swiftly and accurately.
Conclusion

Read More: Fire Extinguishers (APAR): Importance in Environmental Safety
Implementing digital logsheets for safety equipment does come with challenges, ranging from a lack of technological understanding to resistance to change. However, with the right strategies—such as employee training, good budget planning, and selecting the appropriate service provider—these challenges can be overcome. Digital logsheets will provide numerous benefits in terms of efficiency, data accuracy, and enhanced workplace safety. With a more modern and integrated system, companies can reduce the risk of workplace accidents and better ensure employee safety.
leave your comments