In the world of automotive and equipment maintenance industries, efficiency is the key to operational success. Workshops that are inefficient in maintenance management risk losing customers, time, and resources. One way to address this issue is by implementing a digital logsheet, a technology that replaces manual record-keeping systems with an electronic-based system. Digital logsheet has become an essential tool for improving maintenance efficiency in various workshops. With this technology, data recording, monitoring, and analysis become easier and more accurate. This article will discuss how digital logsheets can be implemented in workshops to improve efficiency, the benefits gained, challenges faced, and ways to overcome them.
What is a Digital Logsheet?

Read More: Digital Logsheet: Transparency and Security in Warehouses
A digital logsheet is an electronic record-keeping system designed to manage various operational data automatically and systematically. In the context of a workshop, this technology includes recording service schedules, monitoring vehicle conditions, managing spare parts inventory, and reporting technician performance.
With a digital logsheet, all information can be accessed through software or applications connected to the cloud. This allows workshop owners, managers, and technicians to manage data in real-time without relying on physical documents that are prone to being lost or damaged.
Benefits of Implementing Digital Logsheet
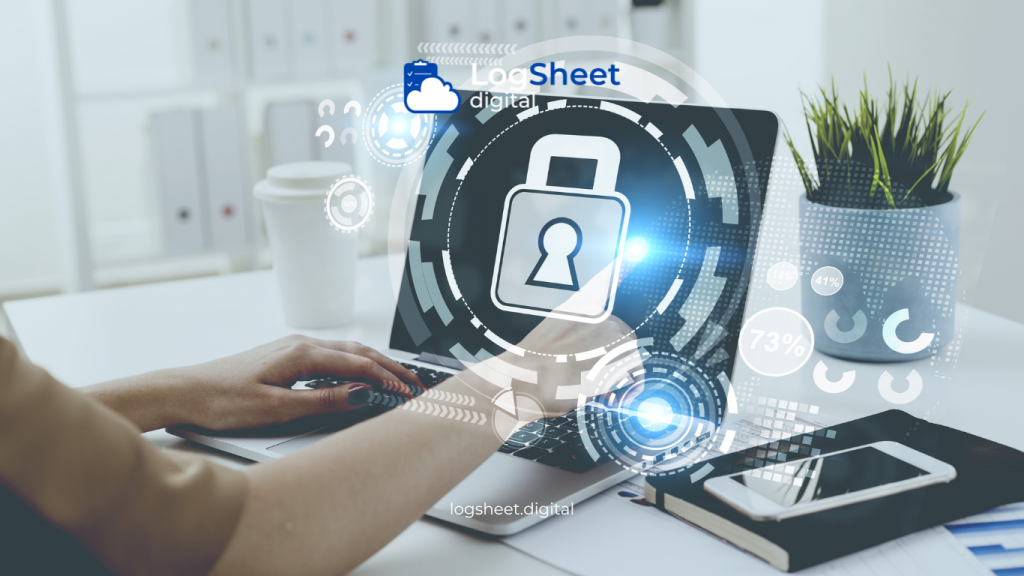
Read More: Sustainability in Safety: How Digital Logsheet Affects the Industry
A digital logsheet provides various benefits that can be directly felt by workshops, including:
1. Improved Data Accuracy
Recording errors often occur in manual systems, such as incorrect data input or loss of documents. With a digital logsheet, recording becomes more accurate because it uses an automated system that minimizes human error.
2. Operational Efficiency
The process of searching for vehicle service data or maintenance schedules becomes faster. Technicians can directly view the vehicle maintenance history, saving time that would have been wasted searching for manual documents.
3. Better Schedule Management
A digital logsheet enables the automatic scheduling of vehicle and equipment maintenance. Notifications will be provided before the deadline, ensuring that no schedule is missed.
4. Easier Data Analysis
With data stored systematically, workshops can analyze trends, such as common types of damage or vehicles that require more intensive care. This information helps improve service quality.
5. Increased Customer Satisfaction
Customers will feel more confident if the workshop has a transparent and professional record-keeping system. Access to vehicle maintenance history also makes communication with customers easier.
How to Implement a Digital Logsheet in a Workshop

Read More: Optimizing Warehouse and Logistics Efficiency with Digital Logsheet
Implementing a digital logsheet requires careful planning to ensure the system functions optimally. Here are the steps that can be taken:
Evaluate the Workshop’s Needs
The first step is to understand your workshop’s specific needs. Is the main issue with schedule management, inventory recording, or data analysis? Choose a digital logsheet with features that meet those needs.
Choose the Right Software
There are many digital logsheet software available in the market. Choose a platform that is easy to use, has good technical support, and fits within your budget. Some software even offers free trials to help you determine the best option.
Provide Training for Staff
Technicians and workshop staff may need time to adapt to the new system. Ensure they receive adequate training to understand how the digital logsheet works.
Integrate with Existing Systems
If your workshop already uses other management systems, make sure the digital logsheet can integrate with them. This will make data flow easier and prevent redundant work.
Monitor and Evaluate Usage
Once the digital logsheet is implemented, monitor the system’s use regularly. Conduct evaluations to ensure that the system is functioning as expected and delivering the desired benefits.
Challenges in Implementing a Digital Logsheet
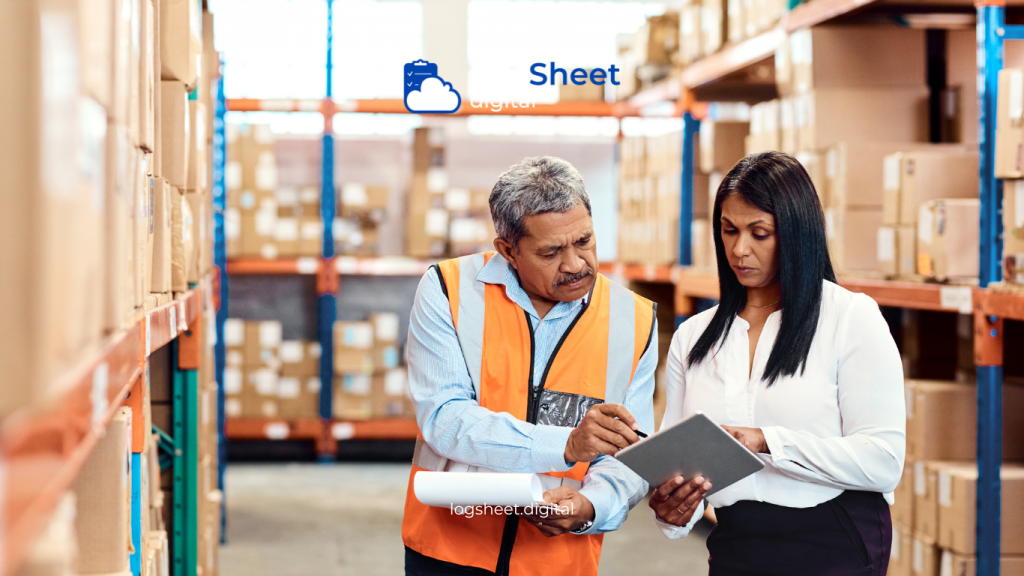
Read More: Optimizing Maintenance Management Through Digital Logsheet in the Workshop Industry
Although it provides many benefits, implementing a digital logsheet also comes with challenges that need to be addressed, such as:
1. Implementation Costs
The initial investment for software, hardware, and staff training may feel expensive for small workshops. However, the long-term benefits of a digital logsheet can help offset these costs.
2. Resistance to Change
Some staff may be reluctant to leave the manual methods they are familiar with. However, this is a common challenge with any technological change, and it can be overcome with proper support and guidance. Additionally, providing clear explanations about the benefits of the new system and involving staff in the transition process can help ease their concerns and facilitate a smoother adaptation.
3. Technical Issues
Technical disruptions, such as poor internet connections or software malfunctions, can hinder the use of the digital logsheet.
4. Data Security
Since digital logsheets store data online, the risk of data leaks or loss due to cyberattacks becomes a major concern.
Solutions to Overcome Challenges

Read More: Digital Logsheet Implementation for Tracking and Monitoring Calibration
To address these challenges, here are some solutions that can be applied:
- Choose an affordable platform: Many digital logsheet software offer pricing packages suitable for small businesses.
- Involve staff from the beginning: Involve staff in the software selection process so they feel responsible for the new system.
- Use regular data backups: Back up data periodically to prevent data loss from technical disruptions.
- Enhance system security: Ensure that the software has security features such as data encryption and two-factor authentication.
Case Study: Success of a Workshop in Implementing Digital Logsheet

Read More: Digital Logsheet Implementation for Improving Quality Supervision Efficiency
A workshop in Surabaya that previously used manual methods to record vehicle service schedules decided to switch to a digital logsheet. After one year of implementation, this workshop reported a 40% improvement in operational efficiency.
Technicians no longer have to search for data manually, allowing them to focus more on repairs. Additionally, customers are more satisfied because vehicle service reports are provided transparently and on time.
This success shows that a digital logsheet is not just a tool for recording data, but a strategic solution to enhance the competitiveness of the workshop.
Conclusion

Read More: Digital Logsheet for More Planned Operational Quality Supervision
Implementing a digital logsheet is an important step for workshops that want to improve vehicle and equipment maintenance efficiency. With more accurate, automated, and integrated record-keeping systems, digital logsheets help optimize workshop operations, increase customer satisfaction, and maximize profits.
Although there are challenges in its implementation, the benefits it provides far outweigh them. With proper planning and strategy, a digital logsheet can be an investment that brings positive change to your workshop.
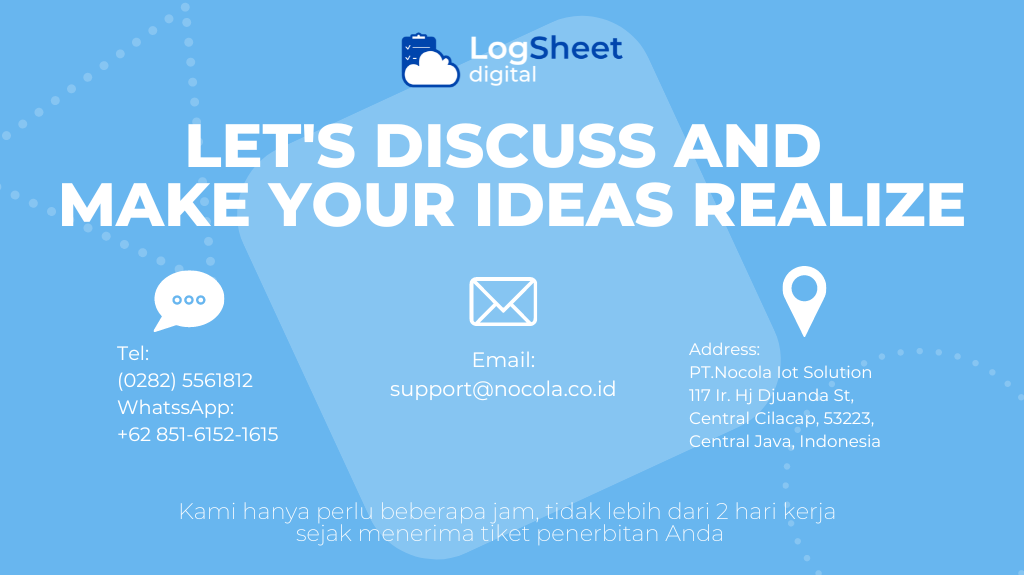
leave your comments