Improving efficiency and workplace safety is a primary focus across various industries. One modern solution that can help achieve this is the use of digital logsheets to monitor data and analyze the performance of safety equipment. This article discusses the benefits, key components, and steps for implementing digital logsheets to ensure optimal performance of safety equipment.
Benefits of Digital Logsheets in Data Monitoring
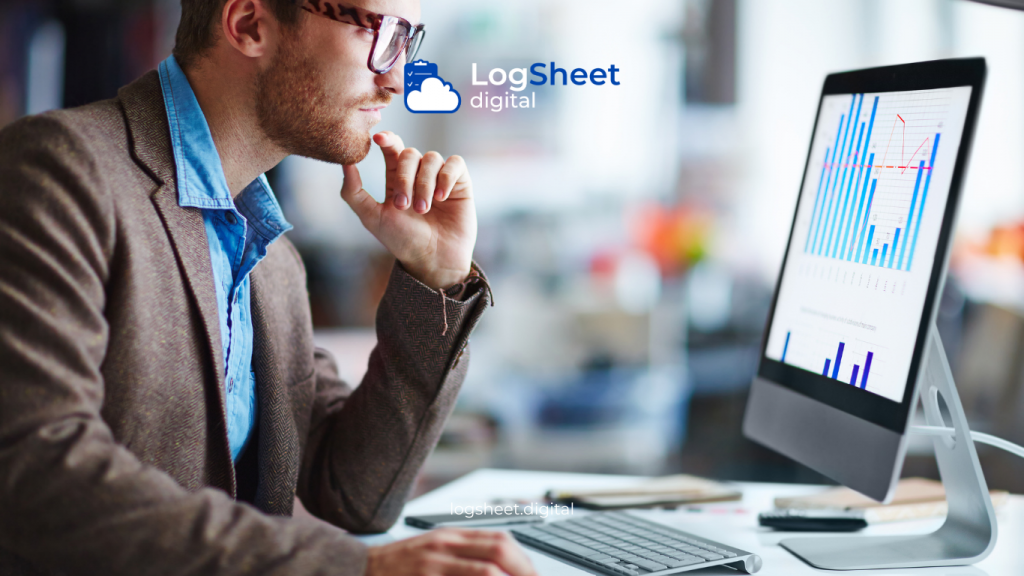
Read More: Logsheet Digital: Transparency and Security in Warehouses
Efficiency in Data Collection
Digital logsheets replace manual methods, allowing data to be collected and stored automatically. This reduces the risk of human error and speeds up the data collection process.
Real-Time Monitoring
With digital logsheets, data can be monitored in real-time. Companies can instantly detect anomalies or malfunctions in safety equipment and take quick action.
Deeper Data Analysis
Data collected digitally is easier to process and analyze. This allows companies to make data-driven decisions regarding maintenance, repairs, or replacement of safety equipment.
Key Components of Digital Logsheets
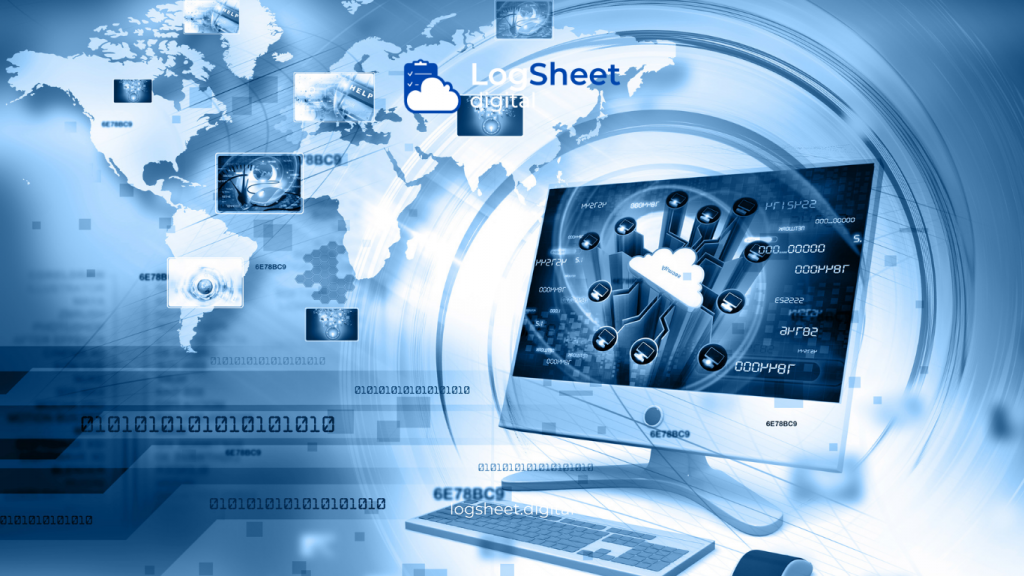
Read More: Sustainability in Safety: How Digital Logsheets Impact Industry
Sensors and IoT Devices
Sensors connected to IoT devices play an essential role in automatically collecting data from safety equipment.
Integrated Data Storage System
Cloud systems or local servers serve as secure, easily accessible data storage.
Analytics Software
Analytics software allows data processing to identify trends, patterns, and potential issues in safety equipment.
User Dashboard
An intuitive user interface helps operational and management teams easily monitor the performance of safety equipment.
Steps to Implement Digital Logsheets
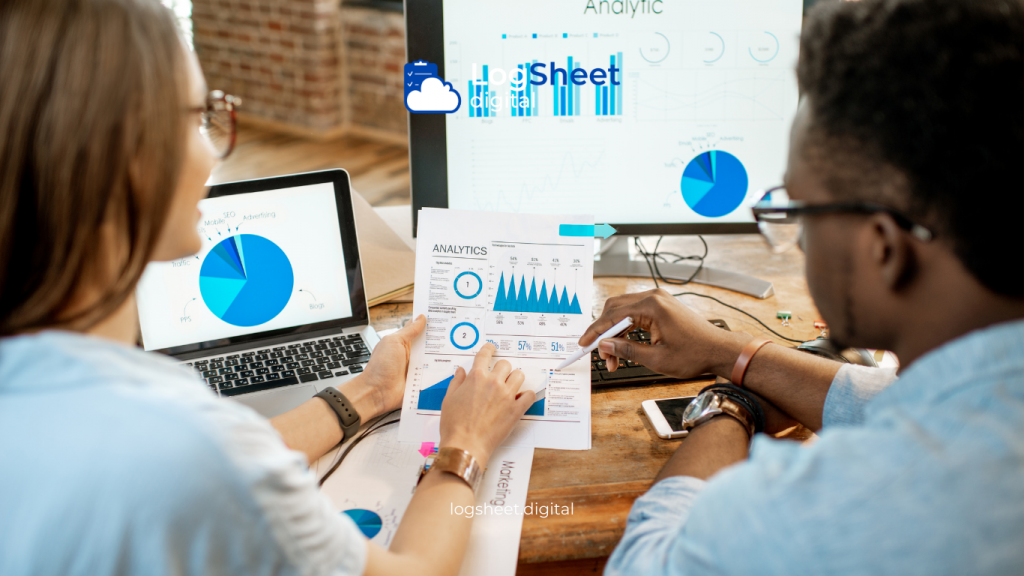
Read More: RFID: Technology Changing the World of Business and Logistics
1. Assess Equipment Needs
Identify the needs and priorities in monitoring safety equipment, such as gas detectors, fire alarms, or personal protective equipment.
2. Choose the Right Technology
Select a digital logsheet compatible with the safety equipment used and features that meet the company’s needs.
3. Integrate with Existing Systems
Ensure the digital logsheet can be integrated with existing safety management systems, such as ERP or CMMS.
4. User Training
Provide training for operational staff to maximize the use of the digital logsheet.
5. Monitoring and Evaluation
Conduct regular monitoring of the digital logsheet system’s performance and periodically evaluate its effectiveness.
Case Studies: Digital Logsheets in Industry

Read More: Optimize Asset Maintenance with Digital Logsheets
Case Study 1: Oil and Gas Company
An oil company used digital logsheets to monitor the performance of gas leak detectors. As a result, gas leak incidents were minimized, and response times to danger warnings became faster.
Case Study 2: Manufacturing Industry
In the manufacturing industry, digital logsheets were used to monitor personal protective equipment such as helmets and masks. Data from the logsheets helped ensure that the equipment was always in good condition.
Challenges in Implementing Digital Logsheets

Read More: Improving Efficiency with Digital Logsheets: Maintenance Implementation Guide
1. Initial Implementation Costs
Acquiring hardware, software, and user training requires significant initial investment.
2. Data Security
Since digital logsheets are cloud-based, there is a risk of data breaches, which must be mitigated with adequate cybersecurity solutions.
3. Resistance to Change
Some employees may be reluctant to switch from manual methods to digital systems. Effective communication and training approaches can address this challenge.
The Future of Digital Logsheets

Read More: Improving Accuracy and Consistency of Calibration with Digital Logsheets
With the development of technology, digital logsheets are expected to become more advanced, such as integration with AI and blockchain technology to ensure data accuracy and transparency. Additionally, 5G connectivity will enable faster and more efficient monitoring of safety equipment.
Conclusion
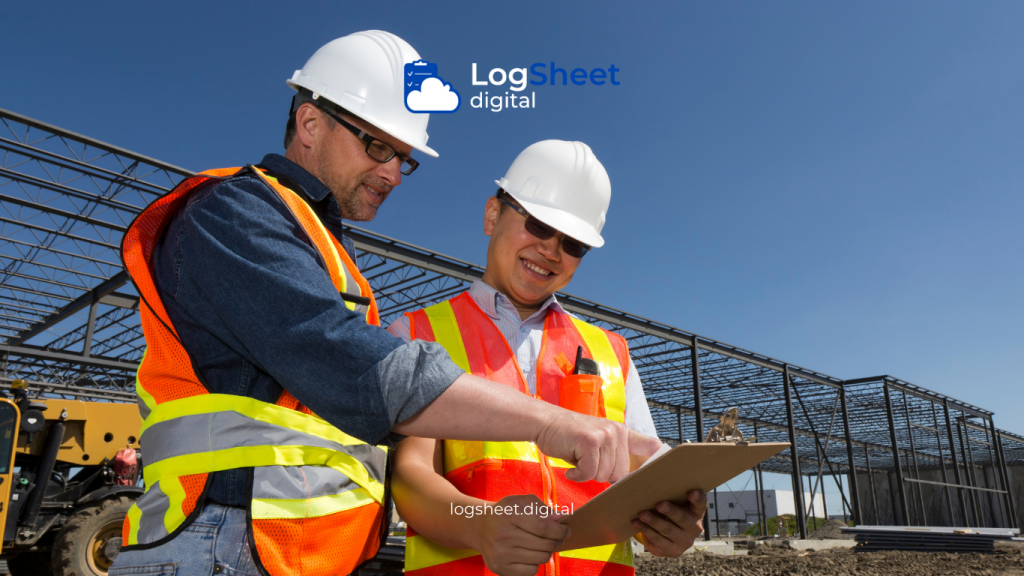
Read More: Advantages of Digital Logsheets in Quality Maintenance Management
The use of digital logsheets in data monitoring and performance analysis of safety equipment provides numerous benefits, ranging from operational efficiency to enhanced workplace safety. Despite the challenges in implementation, this solution represents a step forward towards more modern and effective safety management. Companies that invest in digital logsheets not only improve regulatory compliance but also create a safer and more productive work environment.

leave your comments