In the logistics industry, equipment maintenance is a crucial aspect for ensuring smooth operations and efficiency. Equipment such as vehicles, transport machines, and warehouse tools require regular maintenance to prevent damage that can hinder the logistics process. However, manual maintenance management is often time-consuming, prone to errors, and inefficient. This is where the role of digital logsheets becomes essential. This article will discuss the application of Digital Logsheet for Logistics Equipment management, its benefits, and the challenges that may be faced.
1. What is a Digital Logsheet?

Read More: Implementing Digital Logsheet in Logistics Risk Management
A digital logsheet is a digital recording system used to track and manage operational data, including equipment maintenance. Previously, maintenance records were kept manually on paper; with a digital logsheet, all data is recorded and stored on a cloud-based platform that can be accessed in real-time by all relevant parties.
In the context of logistics equipment maintenance, digital logsheets allow for automatic recording of equipment conditions, the last maintenance time, the next maintenance schedule, and damage reports. This facilitates logistics managers in managing their equipment and reduces the risk of operational disruptions due to poorly maintained equipment.
2. Why is Equipment Maintenance in Logistics Important?

Read More: Enhancing Security and Quality of Deliveries: Digital Logsheet in Logistics
Equipment maintenance in logistics is a crucial step in maintaining operational reliability and efficiency. Without proper maintenance, equipment such as trucks, forklifts, and warehouse systems can experience unexpected failures, leading to delays, additional costs, or even safety risks. Some important reasons for equipment maintenance include:
- Reducing Downtime: Unmaintained equipment can break down during operations, causing downtime and disrupting the logistics flow.
- Extending Equipment Life: Regular maintenance can prolong equipment lifespan, thus reducing replacement costs.
- Enhancing Safety: Well-maintained equipment reduces the risk of workplace accidents, which can harm the company financially and reputationally.
- Operational Efficiency: Equipment functioning optimally will enhance operational efficiency, speed up distribution processes, and minimize delays.
3. Benefits of Digital Logsheet in Logistics Equipment Maintenance Management

Read More: Enhancing Delivery Certainty: Advantages of Digital Logsheet in Warehousing and Logistics
The application of digital logsheets in logistics equipment maintenance offers several significant benefits:
a. Automation and Efficiency
Digital logsheets allow for automation in recording and reporting equipment maintenance. Automatic reminders for routine maintenance can be set up, reducing the risk of forgetting maintenance schedules. With data integrated into one platform, maintenance teams can quickly access the necessary information without having to search through time-consuming manual records.
b. Real-Time Access
With digital logsheets, information about equipment conditions and statuses can be accessed in real-time from various locations. Logistics managers can easily monitor when equipment was last serviced, whether there are issues that need immediate attention, and when the next maintenance is scheduled. This enables faster and more accurate decision-making.
c. Reduction of Manual Errors
Manual maintenance is often susceptible to human errors, such as incorrect recording or loss of important information. With digital logsheets, all data is automatically recorded and securely stored in the system, thus reducing errors that can disrupt equipment maintenance.
d. Enhanced Safety
Digital logsheets allow for detailed recording of equipment conditions and maintenance actions taken. This is essential to ensure that all logistics equipment is functioning properly and is safe to use. Well-documented maintenance can help identify potential safety risks before they impact operations.
e. Data for Performance Analysis
Data collected from digital logsheets can be used to analyze equipment performance. Maintenance managers can observe trends and patterns, such as increasing repair frequencies or parts of equipment that frequently fail. From this data, companies can make strategic decisions to replace frequently malfunctioning equipment or update maintenance plans.
4. Steps in Implementing Digital Logsheet

Read More: Integrating Fleet for Efficiency: Implementing Digital Logsheet in Logistics
Here are some important steps in implementing digital logsheets for logistics equipment maintenance management:
a. Identify Needs
The first step is to identify the specific needs of the company regarding equipment maintenance. Is the focus on tracking vehicle conditions, warehouse equipment, or production machines? By knowing these needs, companies can select the appropriate digital logsheets solution.
b. Choose the Right Logsheet Solution
Once needs are identified, companies must choose the digital logsheets solution that best fits their requirements. Many digital logsheets platforms offer various features, such as integration with other systems, analytical capabilities, and flexibility in setting maintenance reminders.
c. User Training
The digital logsheets system will only be effective if used correctly. Therefore, training employees involved in equipment maintenance is crucial. They need to understand how to input data, monitor equipment conditions, and take action based on the information available in the logsheets.
d. Evaluation and Adjustment
After implementing the digital logsheets, regular evaluations are necessary to ensure the system is running as planned. If there are obstacles or discrepancies, companies can make adjustments to maximize the benefits of using the system.
5. Challenges in Implementing Digital Logsheet

Read More: Digital Logsheet in Improving Logistics Performance and Cost Reduction
Although digital logsheets offer various benefits, their implementation in logistics equipment maintenance management also presents challenges that need to be addressed:
a. Implementation Costs
The initial costs for implementing digital logsheets can be a barrier for some companies, especially small or medium-sized ones. Investment in hardware, software, and employee training requires careful budget planning.
b. Technology Limitations
Some companies may face technology limitations, especially if they operate in areas with unstable internet access. Digital logsheets that rely on the cloud require reliable connectivity to function properly.
c. Resistance to Change
Employees accustomed to manual systems may feel uncomfortable transitioning to digital logsheets. Companies need to ensure they provide adequate training and support for a smooth transition.
6. Case Study: Implementation of Digital Logsheet in a Logistics Company

Read More: Digital Logsheet as a Foundation for Smart Warehousing and Logistics
For example, a large logistics company in Europe successfully implemented digital logsheets to manage the maintenance of their vehicle fleet. Before using digital logsheets, they often faced delays in vehicle maintenance and recording errors, leading to sudden breakdowns and increased repair costs.
After implementing digital logsheets, the company was able to reduce vehicle downtime by up to 25% and significantly improve operational efficiency. Automatic reminders for vehicle maintenance helped the maintenance team keep equipment in optimal condition, thus reducing the risk of disruptions in goods delivery.
7. Long-Term Benefits of Implementing Digital Logsheet
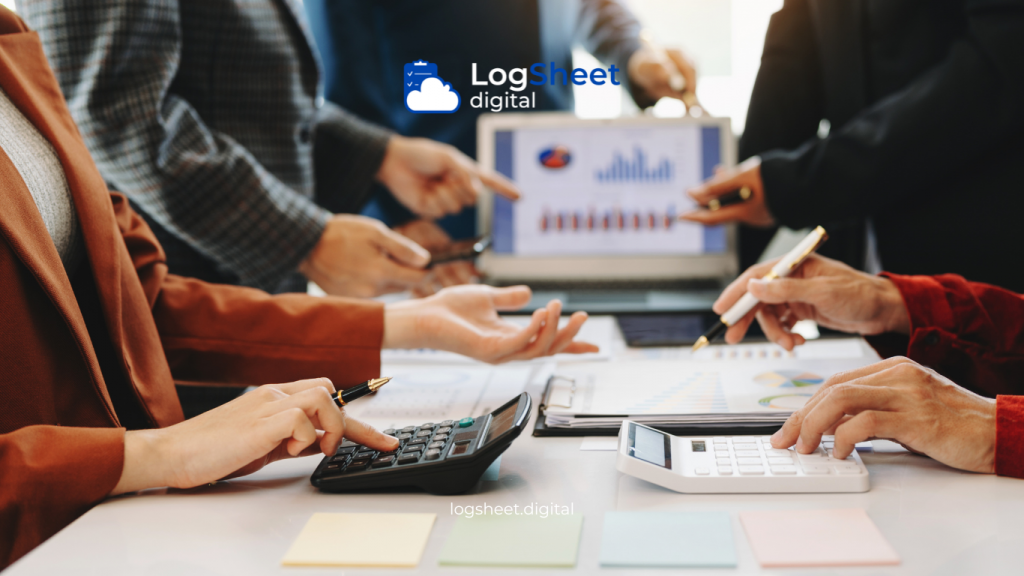
Read More: Overcoming Implementation Challenges of Digital Logsheet in Logistics Environments
In the long run, the implementation of digital logsheets in logistics equipment maintenance management provides significant advantages. In addition to improving efficiency and reducing manual errors, companies also gain better visibility into the conditions of their equipment. The data collected from digital logsheets can be used for better decision-making and more strategic planning, including regarding the replacement of inefficient equipment.
Conclusion
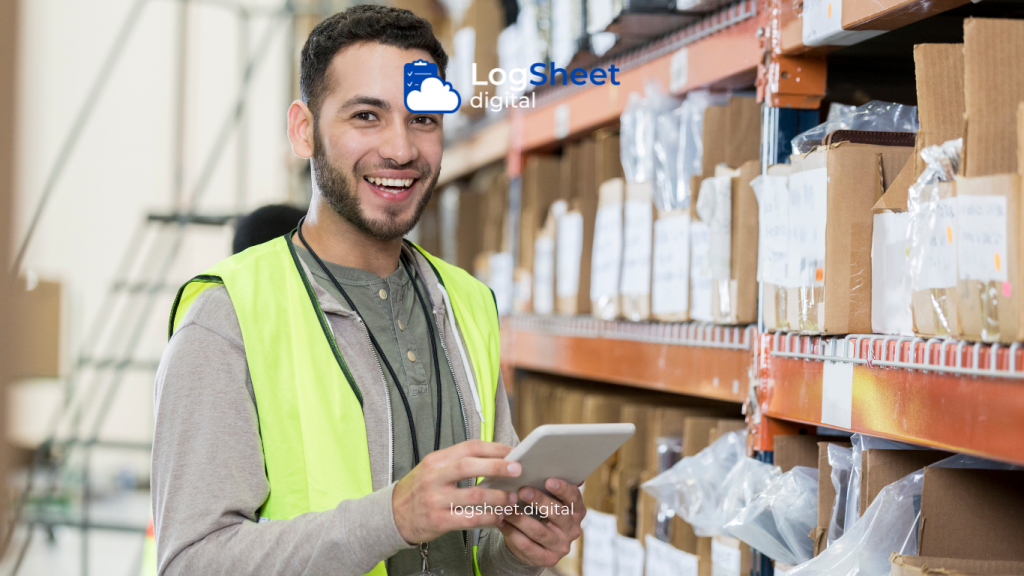
Read More: Logistics Management System with Digital Logsheet
The implementation of digital logsheets in logistics equipment maintenance management brings many significant benefits. With automation, real-time visibility, and reduction of manual errors, companies can enhance operational efficiency and reduce the risk of equipment damage. Although there are challenges such as implementation costs and employee adaptation, the right strategies can help companies overcome these obstacles. In the long term, digital logsheets offer a smarter and more structured maintenance solution, providing a competitive advantage in an increasingly competitive logistics industry.
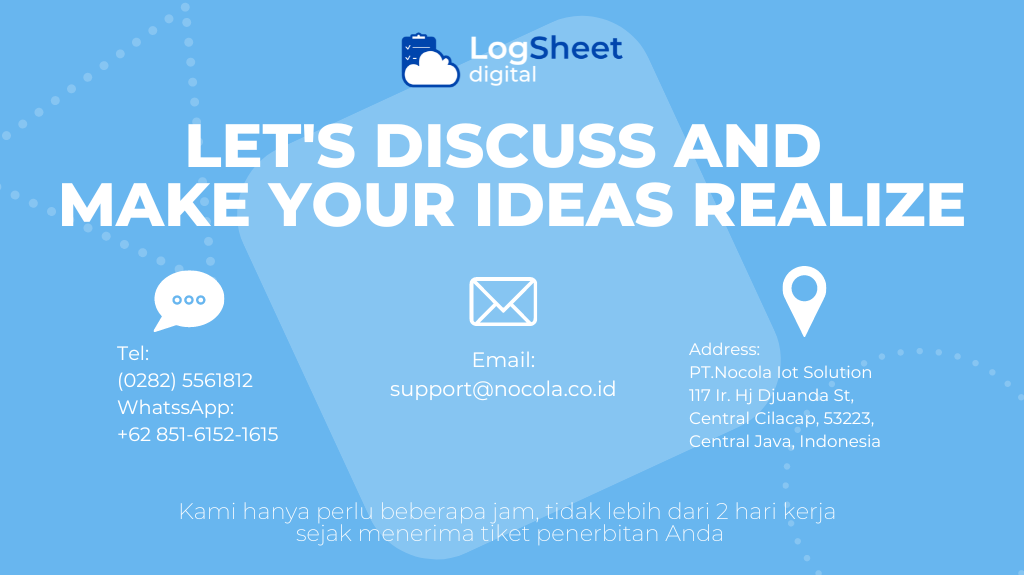
leave your comments