Workplace safety is an aspect that cannot be overlooked in various industries. In emergency situations or accidents, speed and accuracy in reporting are crucial elements for minimizing loss impact and ensuring proper follow-up actions. Traditional recording systems are often slow and prone to errors. Therefore, digital logsheets have emerged as a modern solution to support efficiency in accident reporting, especially concerning safety equipment. This article will discuss the importance of digital logsheets, their benefits, how to implement them, and potential challenges.
The Importance of Fast and Accurate Reporting in Workplace Safety

Read More: Data Security in Digital Logsheet: Challenges and Security Strategies
Accident reporting is a crucial step in ensuring workplace safety. Some reasons why fast and accurate reporting is so important include:
- Quick Response: Timely information helps safety teams respond more effectively.
- Accident Cause Analysis: Complete and structured data simplifies investigations.
- Improvement of Safety Procedures: Documented accident records can be used to identify gaps in existing procedures.
- Regulatory Compliance: Many industries are legally required to record and report accidents in detail.
However, manual systems are often inefficient as they require more time to record, collect, and analyze data. This is why digital logsheets become a better solution.
What is a Digital Logsheet in Safety Equipment?
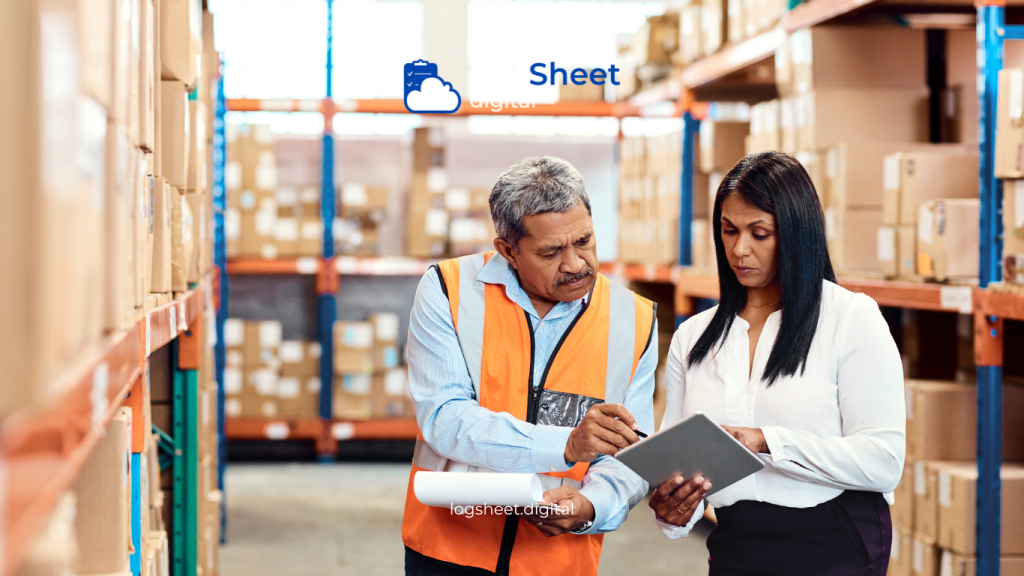
Read More: Safety Equipment Monitoring: Why It’s Important?
A digital logsheet is a technology-based recording system used to log, monitor, and analyze safety data in real-time. In the context of safety equipment, digital logsheets allow the recording of data such as:
- Status and condition of safety equipment.
- Inspection and maintenance schedules.
- Accident details involving safety equipment.
- Follow-up actions after incidents.
By using connected software or apps, digital logsheets enable companies to manage reporting more efficiently and transparently.
Benefits of Digital Logsheet in Accident Reporting
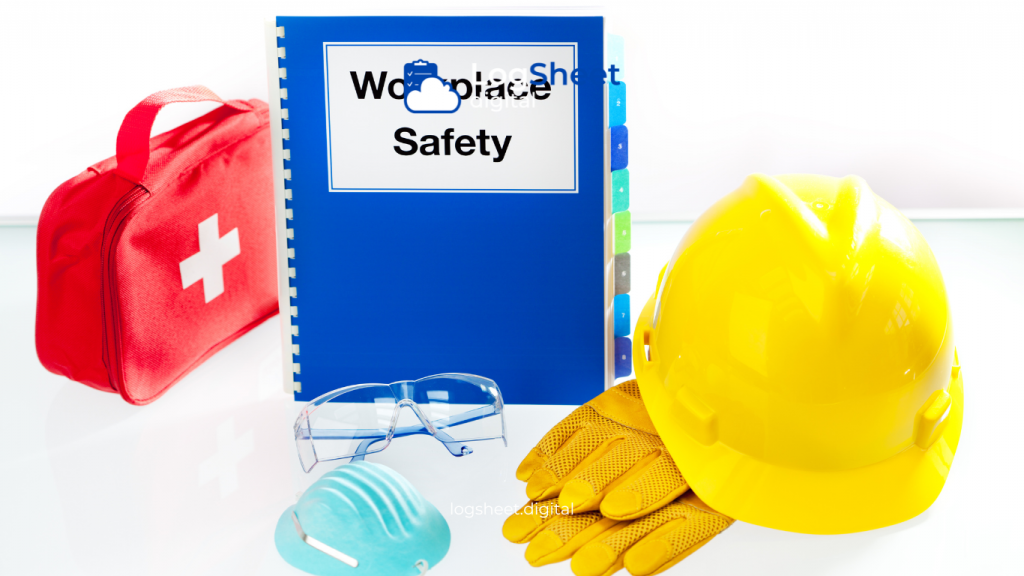
Read More: Logistics Management System with Digital Logsheet
The use of digital logsheets brings significant benefits in accident reporting:
1. Fast Reporting
Digital logsheets allow for instant recording of accident data, reducing reporting time. Information can be accessed immediately by relevant parties, such as management or safety teams.
2. Accurate Data
With an automated system, the risk of manual errors, such as miswriting or data loss, can be minimized.
3. Real-Time Monitoring
Digital logsheets allow for real-time monitoring of safety equipment conditions, providing early warnings if potential issues arise.
4. In-Depth Data Analysis
The system stores historical data that can be analyzed to identify accident patterns and prevent similar occurrences in the future.
5. Regulatory Compliance
Digital logsheets facilitate the auditing process and reporting to authorities by providing complete and structured records.
6. Operational Efficiency
By reducing the time and resources needed to manually collect data, digital logsheets enhance operational efficiency.
Steps to Implement Digital Logsheet in Accident Reporting

Read More: Data Security in Digital Logsheet: Challenges and Calibration Security Strategies
1. Analyze Needs
Identify the company’s needs for accident reporting, such as what data needs to be recorded, required features, and who will access the system.
2. Choose a Digital Logsheet Platform
Select software compatible with the company’s needs. Key features to look for include:
- Real-time recording capabilities.
- Integration with other safety systems.
- Mobile accessibility.
3. User Training
Train employees on how to use the digital logsheet. Focus on how to record, report, and analyze data through the system.
4. Integration with Existing Systems
Integrate the digital logsheet with existing safety procedures to ensure a smooth transition.
5. Testing and Adjustments
Conduct a trial before full implementation. Gather feedback from users to improve the system.
6. Monitoring and Maintenance
Regularly monitor the performance of the digital logsheet and update the software to maintain its reliability.
Challenges in Using Digital Logsheet
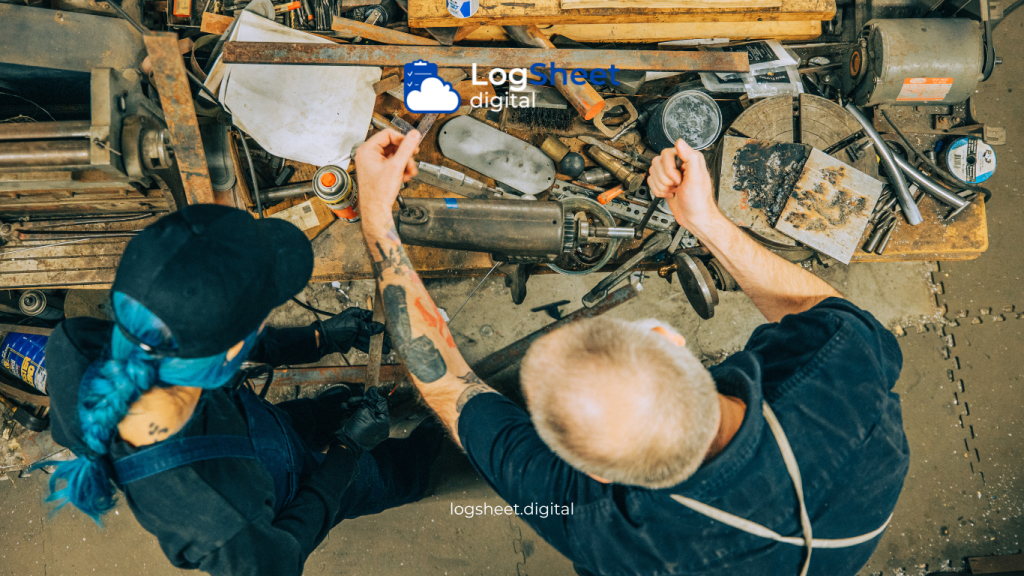
Read More: Effectiveness of Digital Logsheet in Reducing Calibration Defects
Despite its many benefits, implementing digital logsheets also faces challenges such as:
- Employee Resistance:
Some employees may struggle to adapt to the new system. The solution is to provide adequate training and support. - Implementation Costs:
The initial investment for software and hardware can be a barrier, especially for small companies. However, the long-term benefits can offset these costs. - Data Security:
Since data is stored digitally, companies must ensure the system is protected from cyber threats. - Dependence on Technology:
Technical disruptions, such as server failures, can impact data access. Therefore, companies need to have backup systems in place.
Case Study: The Use of Digital Logsheet in the Construction Industry

Read More: Implementing Digital Logsheet in Logistics Risk Management
A large construction company faced challenges in recording workplace accidents involving safety equipment. After implementing digital logsheets, they successfully:
- Reduced accident reporting time from 2 hours to 15 minutes.
- Increased safety regulation compliance to 98%.
- Detected and repaired damaged equipment before accidents occurred.
These results show that digital logsheets are not just a recording tool, but also an effective accident prevention solution.
Conclusion

Read More: Overcoming Challenges in Implementing Digital Logsheet in Logistics Environments
Digital logsheets are an innovation that brings efficiency to accident reporting and safety equipment management. With real-time recording features, in-depth data analysis, and ease of access, digital logsheets help companies improve workplace safety and regulatory compliance.
Although facing challenges like employee resistance or initial costs, the long-term benefits of digital logsheets far outweigh these hurdles. With proper planning and a commitment to adapt, companies can optimize operational efficiency and ensure better employee safety.
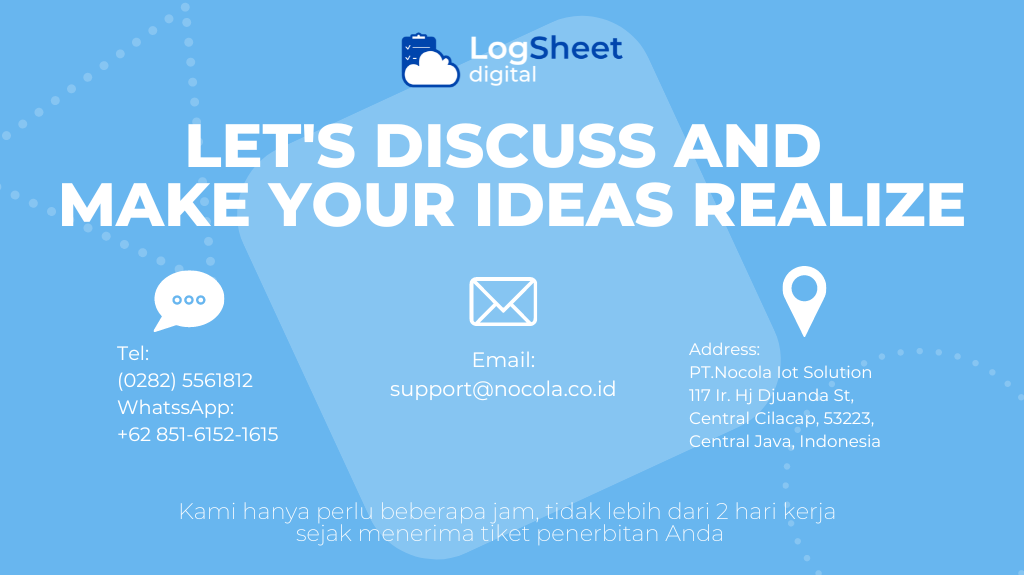
leave your comments