In the competitive automotive industry, workshops need efficient systems to manage and track various aspects of their operations. One increasingly popular solution is the use of digital logsheets. Digital logsheets offer numerous benefits, from performance enhancement to operational cost reduction. This article will explore how Digital Logsheet for Workshopsand help in cost reduction, and provide a practical guide for their implementation.
What is a Digital Logsheet?

Read More: Efficiency in Accident Reporting: Digital Logsheets in Safety Equipment
Definition and Basic Concept
A digital logsheet is an electronic version of traditional paper logsheets used to record various activities and important data in a workshop. Unlike paper logsheets, digital logsheets use software and applications to store and manage information electronically. This allows for easier data access, automated reporting, and integration with other systems.
Key Components of Digital Logsheets
Digital logsheets typically include several key components, such as:
- Digital Forms: Spaces to input relevant data like maintenance schedules, job status, and customer notes.
- Database: A storage place for data that allows searching, filtering, and analyzing information.
- Dashboard: An interface that displays information concisely and understandably, enabling real-time performance monitoring.
Benefits of Digital Logsheets for Workshops

Read More: Real-Time Quality Monitoring: The Role of Digital Logsheets in Production Control
Operational Performance Improvement
1. More Accurate Recording and Reporting
Digital logsheets reduce the likelihood of human error in data recording. With automated systems processing and storing information, workshops can minimize data entry mistakes and loss. Reporting also becomes faster and more accurate, enabling better decision-making based on reliable data.
2. More Efficient Schedule Management
With digital logsheets, managing maintenance and repair schedules becomes easier. The system allows for automatic scheduling and reminders, reducing the risk of delays and ensuring all tasks are completed on time. This improves operational efficiency and maximizes workshop resource utilization.
3. Easy Data Access
Information stored in digital logsheets can be accessed from anywhere, provided there is an internet connection. This makes it easier for technicians and managers to view and update data in real time, even when they are not at the workshop. Easy data access also supports better communication among team members and enhances collaboration.
Reduction in Operational Costs
1. Reducing Paper and Administrative Costs
Using digital logsheets reduces the need for paper and administrative costs associated with managing physical documents. By eliminating the need to print, store, and archive paper logsheets, workshops can save on operational costs and reduce their environmental impact.
2. Efficiency in Resource Usage
Digital logsheets enable better management of workshop resources such as equipment and spare parts. Integrated and centralized data makes it easier to monitor resource usage, reducing waste and improving efficiency. For example, information on available spare parts and maintenance needs can be better managed, avoiding over-purchasing or stock shortages.
3. Reduction in Error Costs
Errors in recording or reporting can result in additional costs, both in terms of wasted time and repair expenses. With digital logsheets, the likelihood of errors is significantly reduced, thus lowering costs associated with operational mistakes. The system also provides faster and more accurate reporting, preventing financial losses that may arise from data inaccuracies.
Implementing Digital Logsheets in Workshops
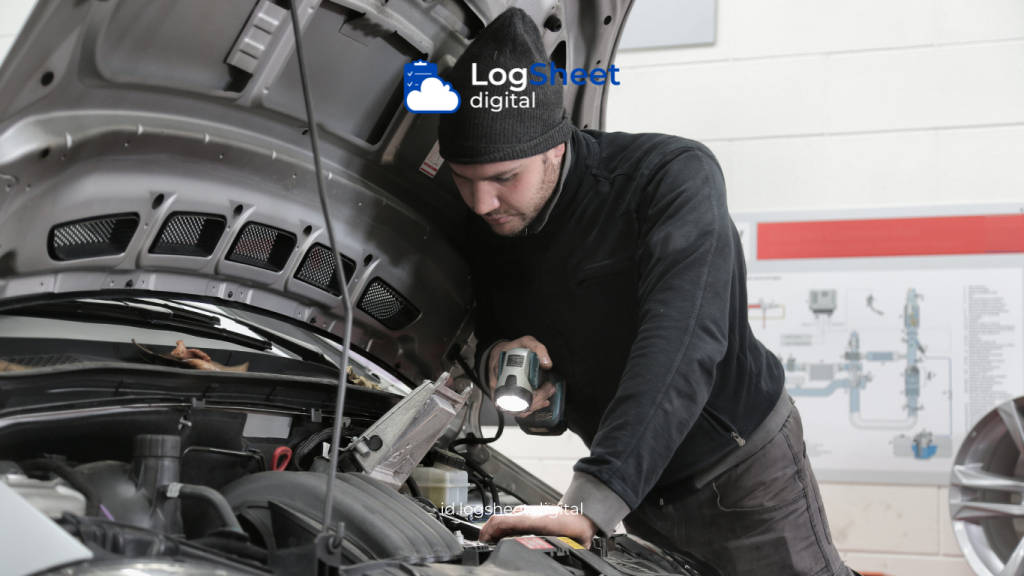
Read More: Enhancing Quality Supervision with Digital Logsheets: Workshop Industry Case
Steps for Implementation
1. Evaluate Needs
The first step in implementing digital logsheets is to evaluate the workshop’s needs. Identify operational aspects that can be improved with digital logsheets, such as maintenance recording, reporting, and inventory management. This evaluation will help in selecting the right software solution.
2. Select the Right Software
Choose digital logsheets software that meets the workshop’s needs. Key features to consider include ease of use, integration capabilities with other systems, and technical support. Ensure that the selected software can fulfill all operational requirements of the workshop.
3. Staff Training
Training staff is crucial to ensure they can effectively use the digital logsheets system. Provide training that covers all aspects of software usage, including data entry, report generation, and information management. Proper training will help staff adapt to the new system and maximize its benefits.
4. Integration with Other Systems
If the workshop is already using other systems, such as inventory management or accounting, ensure that the digital logsheets can be integrated with these systems. Integration allows for seamless data flow between systems, improving efficiency and accuracy.
5. Monitoring and Evaluation
After implementation, regularly monitor and evaluate the digital logsheets system to ensure it functions well. Gather feedback from staff and make improvements as needed. This evaluation will help identify areas for enhancement and ensure that the system provides maximum benefits.
Case Studies of Digital Logsheets Implementation
1. Workshop A: Enhancing Schedule Efficiency
Workshop A implemented digital logsheets to manage vehicle maintenance schedules. With this system, they could automatically schedule maintenance and send reminders to customers. As a result, Workshop A experienced a decrease in maintenance delays and an increase in customer satisfaction.
2. Workshop B: Reducing Inventory Costs
Workshop B used digital logsheets to manage spare parts inventory. The data generated from this system allowed them to better monitor spare parts usage and avoid over-purchasing. Consequently, Workshop B managed to reduce inventory costs and improve operational efficiency.
Challenges in Using Digital Logsheets

Read More: Digital Logsheets as a Pillar Towards Industry 4.0 Quality
1. Initial Implementation Costs
The initial cost of purchasing digital logsheets software and the required hardware can be a challenge, especially for small workshops. However, the long-term benefits of operational efficiency and cost reduction can outweigh the initial investment.
2. Learning Curve
Transitioning from paper logsheets to digital can require time and effort. Staff may need time to adapt to the new system and learn how to use the software effectively. Adequate training support can help overcome this learning curve.
3. Data Security
With electronic data storage, it is important to ensure that the data in digital logsheets is protected from cyber threats. Implement appropriate security measures, such as data encryption and access controls, to safeguard sensitive information.
Conclusion

Read More: Successful Steps in Implementing Digital Logsheets in Quality Control
Summary
Digital logsheets are a valuable tool in enhancing workshop performance and reducing operational costs. By providing accurate recording and reporting, efficient schedule management, and easy data access, digital logsheets help workshops improve operational efficiency and cut costs. Implementing digital logsheets requires needs evaluation, selecting the right software, staff training, and system integration.
Importance of Digital Logsheets Implementation
Implementing digital logsheets not only improves workshop performance but also offers financial benefits through reduced administrative costs, over-purchasing, and operational errors. With an effective system, workshops can better manage their resources and increase customer satisfaction.
Next Steps
To fully benefit from digital logsheets, workshops should start with a thorough needs assessment, choose appropriate software, and provide adequate training for staff. With proper planning and implementation, digital logsheets can become an effective tool in enhancing workshop performance and reducing operational costs, supporting long-term success in the automotive industry.
By understanding and adopting digital logsheets, workshops can better address operational challenges and leverage opportunities for growth and efficiency.

leave your comments