Safety in industrial environments is a top priority to prevent accidents and ensure safe operations. One effective way to enhance safety is by using digital logsheets for safety equipment. This article will discuss the benefits, challenges, and implementation steps of digital logsheets to improve industrial safety.
What Is a Digital Logsheets?

Read more: Safety Equipment Monitoring: Why It Matters?
A digital logsheets is a software-based tool that replaces manual recording methods with an electronic system. In the context of industrial safety equipment, digital logsheets are used to record, track, and manage information related to inspections, maintenance, and the condition of safety equipment.
Benefits of Digital Logsheets for Safety Equipment
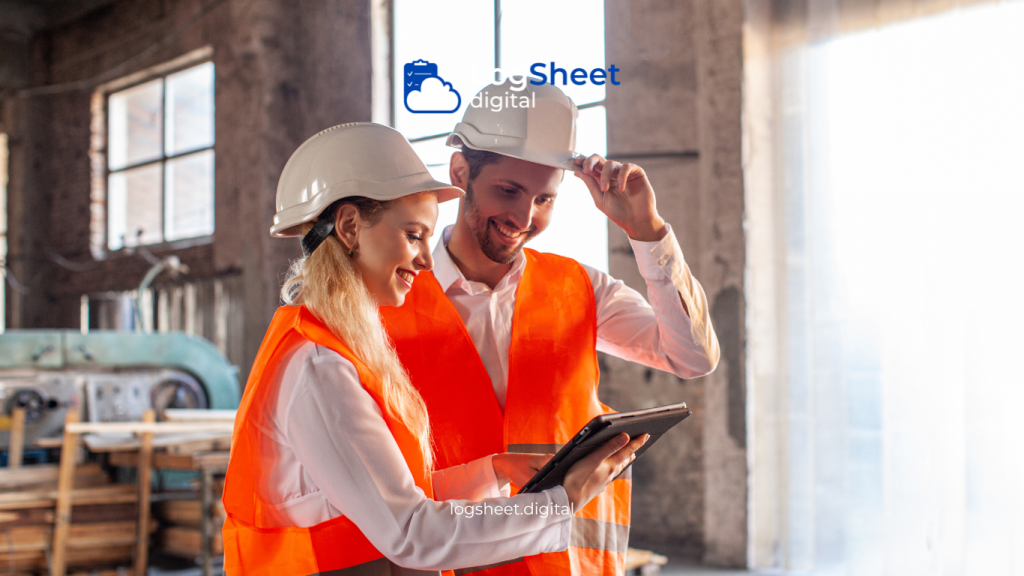
Read more: Advantages of Digital Logsheets in Equipment Safety
Higher Data Accuracy
With digital logsheets, data is recorded automatically and in real-time, reducing the risk of human error. This is crucial in ensuring that all safety equipment is always in optimal condition.
Real-Time Access for Decision Making
Data entered into digital logsheets can be accessed in real-time, allowing safety managers to take necessary actions immediately if issues are found with safety equipment.
Increased Efficiency and Productivity
The use of digital logsheets reduces the time needed for manual data entry and retrieval, allowing staff to focus on other more productive tasks.
In-Depth Data Analysis
Digital logsheets provide advanced data analysis tools, enabling companies to identify trends and patterns that can aid in strategic decision-making related to safety.
Data Transparency and Security
Data recorded digitally is easier to track and audit. Additionally, digital logsheets can be protected with passwords and other security systems, reducing the risk of data loss or damage.
Digital Logsheets Implementation: Case Study of PT. Industri Aman

Read more: Digital Logsheets: Safety in the Chemical, Oil, and Gas Industry
Company Background
PT. Industri Aman is a large manufacturing company that faced various challenges related to safety equipment maintenance. Before using digital logsheets, the company used manual recording methods that were often inaccurate and time-consuming.
Challenges Faced
Recording Errors
Errors in manual recording led to data inaccuracies that could result in accidents.
Delayed Information
Delayed information made it difficult for management to take timely preventive actions.
Limited Data Analysis
Manual data analysis did not provide the deep insights needed to improve overall safety.
Digital Logsheets Implementation
System Selection
The company selected digital logsheets software that met their needs, including real-time tracking and data analysis features.
Employee Training
Employees were trained to use the new system and understand how to utilize it optimally to enhance safety.
Integration with Existing Systems
Digital logsheets were integrated with existing operational systems to ensure smooth and comprehensive data flow.
Results of Implementation
Reduction in Errors
Recording errors drastically decreased, improving data accuracy and workplace safety.
Real-Time Data Access
Safety managers could access operational data directly, speeding up decision-making processes.
Time Efficiency
The time required for recording and processing data reduced, increasing staff productivity.
Better Data Analysis
The company could generate more detailed reports and analyses, helping them identify areas for improvement in safety.
Challenges in Implementing Digital Logsheets

Read more: Digital Transformation for the Manufacturing Industry
Initial Investment Requirements
Implementing digital logsheets requires an initial investment in software and hardware. Companies must ensure that this investment provides long-term benefits.
Employee Training
Employee training requires additional time and cost but is crucial for ensuring effective system use.
Data Security
Digital data is vulnerable to threats such as hacking or malware. Companies must have strong security systems to protect their data.
Resistance to Change
Some employees may be reluctant to switch from manual to digital systems. Companies need to manage this change effectively and provide the necessary support.
Steps for Implementing Digital Logsheets
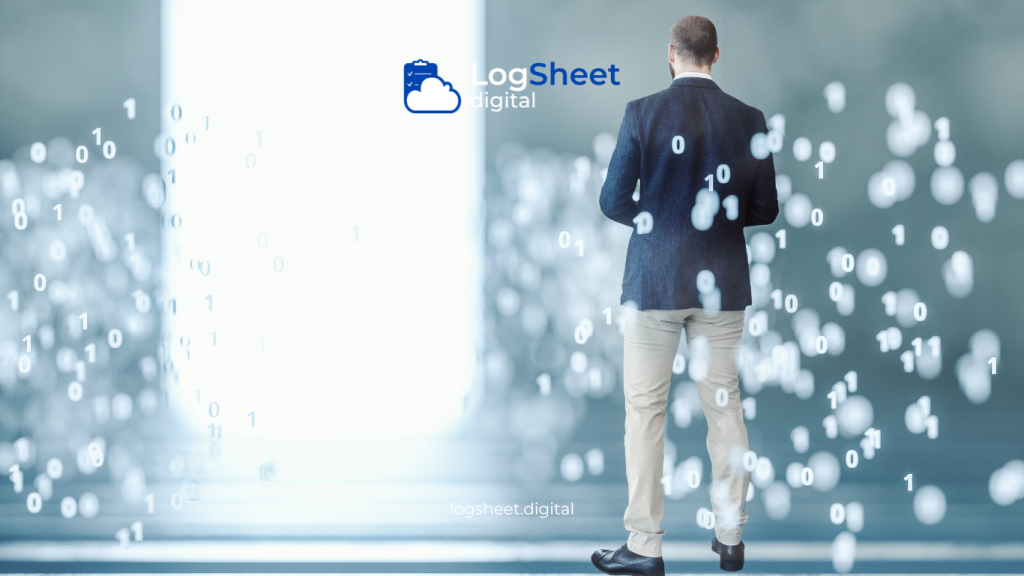
Read more: Benefits of Using Digital Logsheets for Companies and Employees
Identify Company Needs
The first step is to identify the specific needs of the company related to safety equipment.
Choose the Right Software
The company should choose digital logsheets software that fits their needs.
Employee Training and Support
Training should cover how to use the software and utilize data to improve workplace safety.
Monitor and Evaluate the System
After implementation, the company should monitor the use of digital logsheets and evaluate the results.
Conclusion
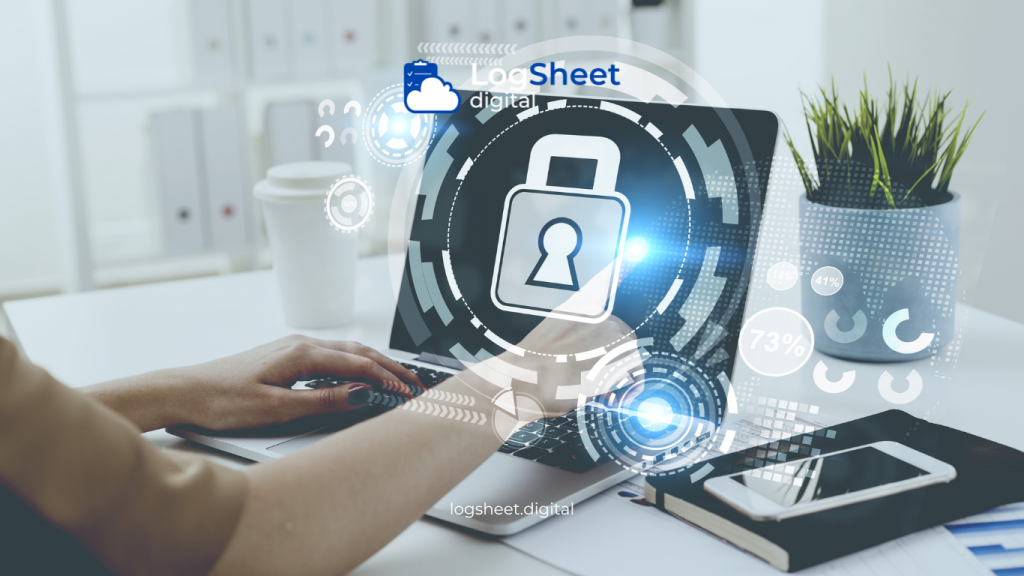
Read more: The Importance of Routine Inspections in Preventing Fatal Accidents
Using digital logsheets for industrial safety equipment can provide significant benefits, including improved data accuracy, time efficiency, and deeper data analysis. Although there are challenges in implementation, with the right steps, companies can enhance workplace safety and overall operations. Digital logsheets represent a strategic investment that can help companies remain competitive and prepared for future challenges in safety.

leave your comments