In an increasingly complex and connected industrial world, efficiency in equipment and machinery maintenance is crucial for maintaining productivity and reducing downtime. By transitioning from manual methods to digital logsheets, companies can optimize their maintenance processes, reduce operational costs, and enhance accuracy and visibility. This article will explore in depth how digital logsheets can improve maintenance efficiency in industry, the benefits they offer, the challenges that may be faced, and the steps for implementation.
What is a Digital Logsheet?

Read more: Digital Logsheets: The Latest Solution for Enhancing Quality Monitoring and Analysis
Digital logsheets are IT-based systems designed to record, track, and analyze maintenance data electronically. Unlike traditional logsheets that often use paper or spreadsheets, digital logsheets offer advanced features that can enhance maintenance efficiency.
Benefits of Digital Logsheets
1. Improved Data Accuracy
One of the primary benefits of digital logsheets is improved data accuracy. By eliminating manual recording processes prone to errors, digital systems ensure that the collected data is accurate and consistent. This is crucial in maintenance, where the accuracy of information can impact decision-making.
2. Real-Time Data Access
Digital logsheets enable real-time data access. Maintenance teams and management can view up-to-date information about maintenance status, equipment condition, and emerging issues. Real-time access speeds up the response to problems and allows for quicker corrective actions.
3. Better Reporting and Analysis
Digital systems can automatically generate reports and perform analyses. Using advanced analytical tools, companies can conduct in-depth data analysis, identify trends, and understand the root causes of issues. This helps in maintenance planning and strategic decision-making.
4. Reduction in Paper and Storage Space
Transitioning from manual logsheets to digital reduces the need for paper and physical storage space. Data is stored electronically, reducing the risk of document loss or damage and simplifying information access and management.
5. More Efficient Collaboration
In industrial environments, collaboration between different departments is vital. Digital recording allows maintenance, engineering, and management teams to work together more effectively by sharing data and information through a common platform. This enhances communication and coordination among teams.
Challenges in Implementing Digital Logsheets

Read more: Digital Transformation in Quality Control: The Role of Digital Logsheets in Industry
Although digital logsheets offer many benefits, their implementation is not always without challenges. Here are some common challenges that may be encountered:
1. High Initial Costs
The initial investment for digital logsheets, including hardware, software licenses, employee training, and potentially IT infrastructure upgrades, can be substantial. Despite the high costs, the long-term benefits of efficiency and cost savings often outweigh the initial investment.
2. Need for Employee Training
Training employees is a crucial aspect of implementing digital recording. Employees need to understand how to use the system effectively, including data entry, report generation, and utilizing other system features. Adequate training is essential to ensure that all users can fully leverage the system.
3. Integration with Existing Systems
Integrating digital logsheets with existing maintenance or other systems like ERP can be challenging. This integration requires careful planning and execution to ensure compatibility and smooth data flow. Integration issues can affect the system’s effectiveness and may require time and resources to resolve.
4. Data Security
Data security is a major concern when transitioning to digital systems. Maintenance data stored electronically must be protected from unauthorized access and potential cybersecurity threats. Digital logsheets must include adequate security features such as data encryption, access controls, and audit trails to safeguard sensitive information.
Steps for Implementing Digital Logsheets

Read more: Improving Quality Control Accuracy with Digital Logsheets
To maximize the benefits of digital logsheets, companies need to follow these implementation steps:
1. Evaluate Needs and Goals
The first step in implementing digital recording is to evaluate the company’s needs and goals. Identify the maintenance processes to be monitored with the digital system and determine the metrics and performance indicators to be used. This helps in selecting the appropriate system and ensuring it meets the company’s specific needs.
2. Choose the Right System
Select digital logsheets software that fits the company’s needs and budget. Consider features such as customization, integration with existing systems, and technical support. Choose a system that is user-friendly, has an intuitive interface, and can be tailored to existing maintenance processes.
3. User Training
Provide adequate training to employees on how to use the digital logsheets. Ensure they understand data entry, report generation, and using other system features. Effective training will facilitate successful system adoption and maximize the benefits gained.
4. Data Migration
Migrate existing maintenance data from the old system to the digital system. This migration must be done carefully to ensure that no data is lost or corrupted. Verify the data after migration to ensure the accuracy and consistency of the transferred information.
5. Monitor and Evaluate
After implementation, regularly monitor to ensure the system functions correctly and provides the expected benefits. Evaluate system performance and identify areas needing improvement or enhancement. Make necessary adjustments to ensure the system continues to meet company needs.
Case Study: Efficiency Improvement in a Manufacturing Plant
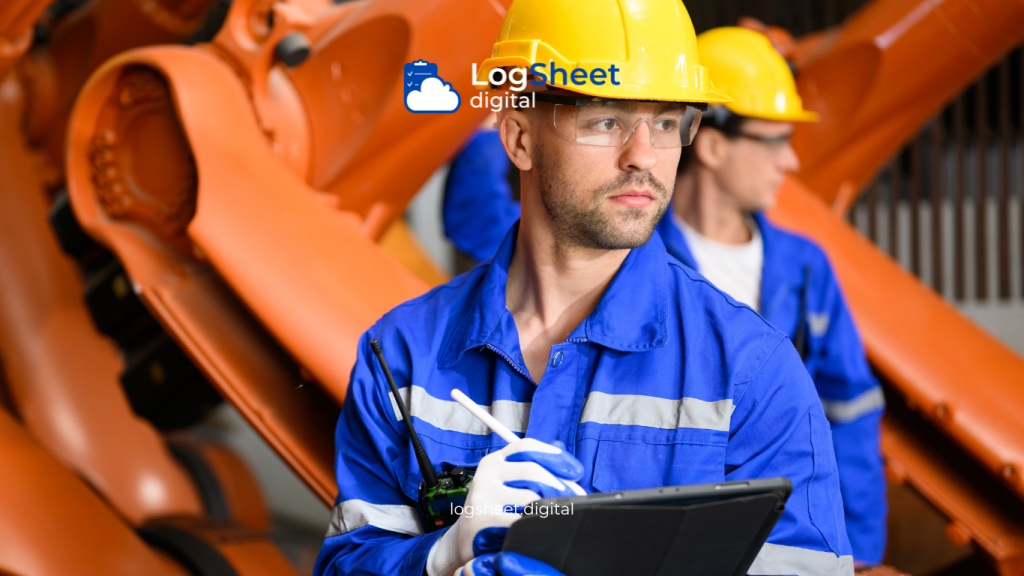
Read more: Optimal Quality: Digital Logsheets & Raw Materials
To provide a real-life example of the benefits of digital recording, let’s look at a case study in a manufacturing plant:
Background
XYZ Factory is a manufacturing company producing various consumer goods. The company faced challenges in managing machinery and equipment maintenance. The manual recording process using paper often led to delays in reporting and data errors. Unexpected downtime and high maintenance costs were major issues faced by the plant.
Solution
To address these issues, XYZ Factory implemented a digital logsheets system. This system replaced the manual method by recording and tracking maintenance data electronically. Each worker on the production line used mobile devices to enter maintenance data in real-time. The collected data was then processed and presented in an easily understandable dashboard for management.
Results
After implementation, XYZ Factory experienced significant improvements in maintenance efficiency:
- Reduction in Maintenance Time: The time required for recording and analyzing maintenance data decreased by up to 50%. By eliminating manual processes, the maintenance team could focus on more critical tasks.
- Improved Data Accuracy: Data entry errors drastically reduced, improving the accuracy of maintenance reports. More accurate data helps in better planning and decision-making.
- Faster Problem Identification: The system detected anomalies in quality data in real-time, allowing issues to be identified and addressed more quickly. This reduced downtime and improved machine availability.
- Reduction in Product Defects: In-depth data analysis allowed the company to identify root causes of quality issues and take corrective actions. This reduced the number of defective products and increased customer satisfaction.
- Increased Customer Satisfaction: Improved product quality directly impacted customer satisfaction and company reputation. Higher customer satisfaction can contribute to business growth and customer loyalty.
Lessons Learned
This case study demonstrates that digital logsheets can significantly enhance maintenance efficiency and product quality. By leveraging IT technology, companies can optimize their business processes and achieve a competitive edge. Implementing digital recording not only modernizes maintenance processes but also provides valuable insights for better planning and decision-making.
Conclusion

Read more: Digital Logsheets: The Latest Solution for Enhancing Quality Monitoring and Analysis
Digital logsheets have proven to be an effective solution for enhancing maintenance efficiency in industry. By replacing manual methods that are often error-prone and time-consuming, digital recording enables more accurate data entry, real-time access, and in-depth analysis. Although challenges in implementation exist, the long-term benefits of this system can provide significant competitive advantages.
Companies adopting digital recording can reduce operational costs, improve machinery reliability, and optimize maintenance processes. Proper implementation steps, including selecting the right system, training employees, and ongoing monitoring, will ensure that the system functions effectively and delivers the expected results.
By embracing this technology, companies not only modernize their maintenance processes but also strengthen their foundation for long-term growth and success. Digital logsheets represent a forward leap in industrial maintenance evolution, and companies leveraging them will find themselves better positioned to tackle future challenges.

leave your comments