In the increasingly advanced industrial era, workplace safety has become a crucial aspect that cannot be overlooked. Safety equipment available at the workplace, such as fire extinguishers, helmets, and personal protective equipment, plays an essential role in preventing incidents and ensuring employee safety. However, ensuring that all safety equipment is functioning properly is not a simple task, especially if monitoring methods are still done manually. A modern solution that is increasingly being adopted is the use of digital logsheets. This system replaces manual logsheet with a digital recording method that is efficient, accurate, and easy to access. With digital logsheet, companies can monitor and supervise the condition of safety equipment in real time, ensuring they are always ready for use when needed.
The Importance of Monitoring Safety Equipment in Modern Industry

Read More: Data Security in Digital Logsheets: Challenges and Security Strategies in Calibration
Modern industries span various sectors that rely on safety equipment to maintain the safety and well-being of employees. Routine monitoring of this equipment is critical because:
- Preventing Workplace Accidents
Safety equipment that is not functioning properly increases the risk of accidents. Regular monitoring ensures that equipment is always in a ready-to-use condition. - Compliance with Safety Standards and Regulations
Many countries have strict regulations regarding workplace safety monitoring. Proper oversight helps ensure compliance with these regulations. - Supporting Productivity and Work Efficiency
When employees feel safe, they can focus better and be more productive. Proper monitoring boosts their confidence in the protection available in the work environment.
Common equipment monitored in industries includes:
- Fire extinguishers
- Gas or chemical leak detection systems
- Ventilation systems for hazardous areas
- Helmets, safety glasses, and other protective body gear
Understanding Digital Logsheets

Read More: Digital Logsheets and Safety Awareness Improvement: A Case Study in Industry
A digital logsheets system is a technology that allows for the electronic recording, monitoring, and supervision of safety equipment. The system can be accessed through devices such as smartphones, tablets, or computers and stores data in the cloud, making it accessible anytime and anywhere by authorized parties. Some of the key features of digital logsheets include:
- Real-Time Recording: Data can be updated and monitored instantly as inspections take place.
- Cloud Integration: Data is automatically stored in the cloud, ensuring there is no risk of losing information.
- Accessibility and Ease of Access: The system can be accessed from various devices, making monitoring more convenient.
- Analytics and Reporting: It simplifies the process for companies to analyze and report data for audit and compliance purposes.
Key Benefits of Digital Logsheets in Safety Equipment Monitoring

Read More: Efficiency in Asset Inventory Management Using Digital Logsheets
The use of digital logsheets for monitoring safety equipment offers numerous benefits for companies, including:
1. Higher Operational Efficiency
Manual recording is time-consuming and prone to errors. Digital logsheets streamline the monitoring process, making it faster, easier, and paperless.
2. Accuracy and Data Reliability
The digital logsheets system reduces the risk of recording errors that are common with manual methods. All entered data is immediately recorded and can be verified.
3. Ease of Reporting and Auditing
Digital logsheets allow for detailed records of equipment conditions, such as when it was last inspected and when the next maintenance is due. This data can be used as evidence during safety audits.
4. Automatic Maintenance Scheduling Reminders
Safety equipment such as fire extinguishers requires regular maintenance. The digital logsheets system can send automatic reminders to the maintenance team when it is time for the next inspection.
5. Transparency and Easy Data Access
With digital logsheets, management can access equipment condition data anytime without having to wait for manual reports. This data helps management make better decisions about equipment maintenance and replacement.
6. Reduction of Paper Use and Environmental Impact
By adopting a digital system, companies can reduce paper usage, contributing to environmental sustainability while saving on printing and storage costs.
Steps for Implementing Digital Logsheets for Safety Equipment

Read More: Digital Logsheets as a Key Factor in the Shift to Logistics 4.0
Implementing digital logsheets requires strategy and preparation. Here are the steps that can be followed:
1. Identify the Company’s Needs
Conduct a needs analysis to determine which safety equipment should be monitored with digital logsheets. Each type of equipment may require different recording specifications.
2. Choose the Right System or Application
Select a digital logsheets application or software that meets the company’s needs. Ensure that the system is compatible with existing devices and can meet the required monitoring requirements.
3. Involve Employees in the Planning Process
Involving employees in the planning and training stages can help ensure a smoother adaptation process and minimize resistance to change.
4. Train Users and Test the System
Training is an essential part of digital logsheets implementation. Ensure all users understand how the system works and are able to use its features effectively.
5. Conduct Trial Runs and Adjustments
Before full deployment, test the system to identify potential issues. This also gives the opportunity to make adjustments as needed.
6. Ongoing Monitoring and Evaluation
Once implemented, regularly evaluate the system to ensure it is functioning as expected. This helps identify areas that may need improvements or updates.
Case Study: Successful Implementation of Digital Logsheets

Read More: Overcoming Challenges in the Implementation of Digital Logsheets on Safety Equipment
To understand the real benefits of digital logsheets, let’s look at a case study from a construction company that successfully implemented this system.
Background
This company has more than 100 active project sites, with hundreds of safety devices on each site, including fire extinguishers and personal protective equipment. The biggest challenge was ensuring these safety tools were always in working order without needing manual inspections.
Implementation of Digital Logsheets
After adopting digital logsheets, the company was able to:
- Monitor the condition of safety equipment in real-time across all project locations.
- Quickly identify equipment that needed maintenance or replacement.
- Achieve a 30% faster efficiency compared to the manual system.
As a result, workplace accidents related to safety equipment decreased significantly, and work efficiency improved.
Challenges in Implementing Digital Logsheets
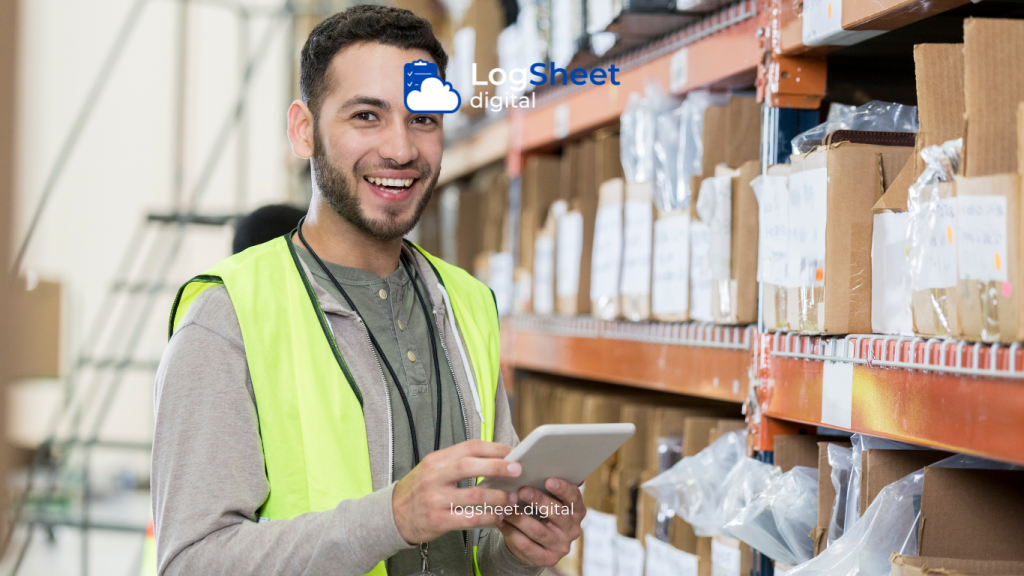
Read More: Overcoming Challenges in Implementing Digital Logsheets for Safety Equipment
Like other technologies, digital logsheets also face several challenges during implementation:
1. Implementation Costs
The costs for devices and training can be a challenge for some companies, particularly small or medium-sized businesses.
2. Connectivity Issues
Digital logsheets rely on a stable internet connection. In some locations, internet connectivity might be a challenge.
3. Employee Resistance to Change
Employees accustomed to manual systems might struggle with or resist switching to digital systems.
4. Data Security
Data stored in the cloud could be vulnerable to cybersecurity threats if not adequately protected.
Overcoming the Challenges in Implementing Digital Logsheets
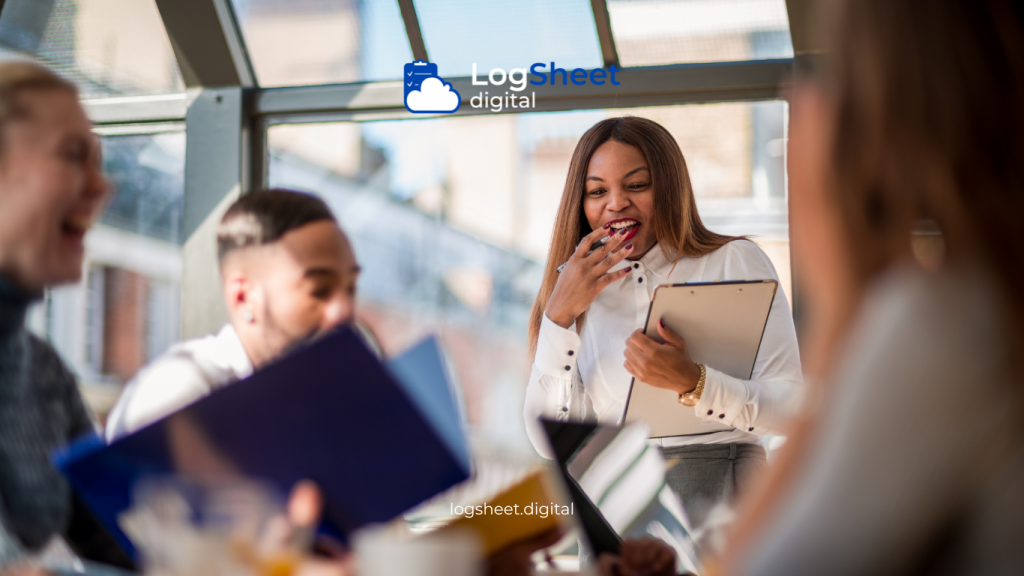
Read More: Applying Digital Logsheets for Monitoring Machine Performance in Operations
Here’s how these challenges can be addressed:
1. Provide Intensive Training
Proper training helps employees become more confident in using the new system.
2. Use Robust Security Systems
Ensure that data is stored in a secure cloud environment to effectively prevent data breaches. By doing so, you not only enhance the protection of sensitive information but also reduce the risk of unauthorized access. Furthermore, using a reliable cloud storage solution ensures that your data is easily accessible while maintaining high levels of security. This way, you can achieve both convenience and safety, safeguarding your data from potential threats.
3. Find Alternative Connectivity Solutions
Consider offline options for digital logsheets in locations with limited internet access.
Conclusion

Read More: Advantages of Digital Logsheets in Quality Management and Compliance in the Manufacturing Industry
The digital transformation of safety equipment monitoring is an essential step for industries aiming to enhance workplace safety, improve efficiency, and reduce operational costs. By utilizing digital logsheets, companies can keep track of the condition of safety equipment, avoid costly mistakes, and ensure compliance with safety standards, all while reducing paper usage and improving overall productivity. Despite some initial challenges, the long-term benefits of implementing digital logsheets far outweigh the difficulties, offering a more efficient, accurate, and secure way to manage safety equipment.

comments (0)