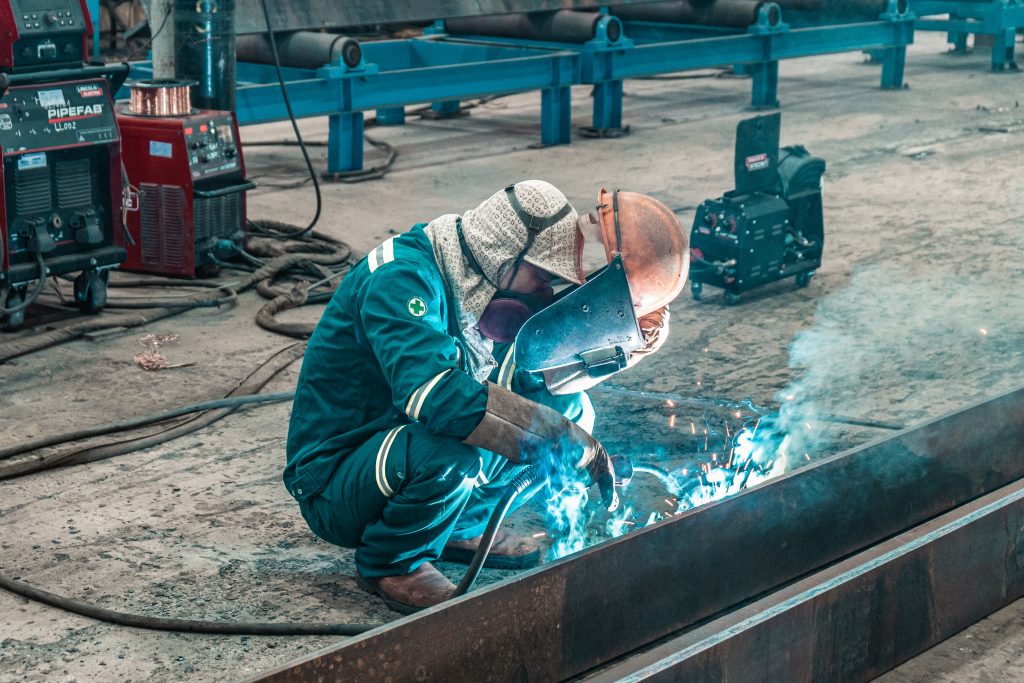
Read also: Digital Logsheets for Increasing Safety in Industry
In the midst of rapid technological developments, the application of this system to safety equipment has become an effective solution in improving equipment monitoring and maintenance. This article will discuss the successful steps in implementing this system in safety equipment, as well as the benefits that can be gained in increasing safety efficiency and reliability.
Needs Analysis and Selection of Digital Logsheet Platforms
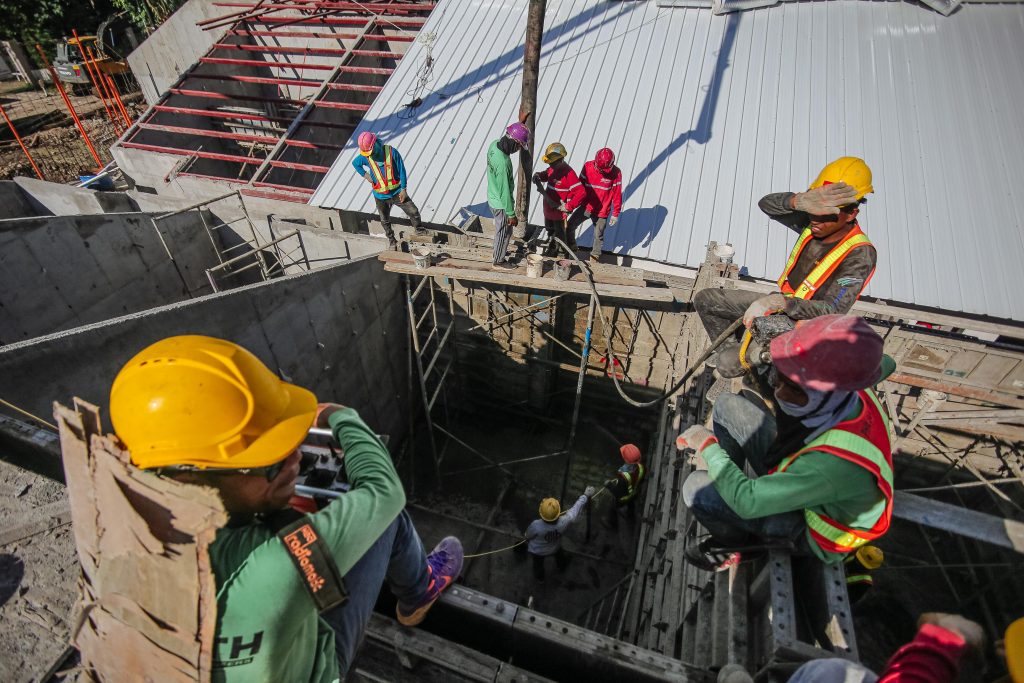
Read also: Digital Logsheet Monitoring Tool Warehouse and Logistics
The first step in implementing a digital logsheet is to carry out an in-depth analysis of the need for safety equipment to be monitored. Identify information that needs to be recorded and monitored periodically. After that, choose this system platform that suits your company and equipment needs. Make sure the platform has adequate security features to protect sensitive data.
Training and Integration with Other Systems
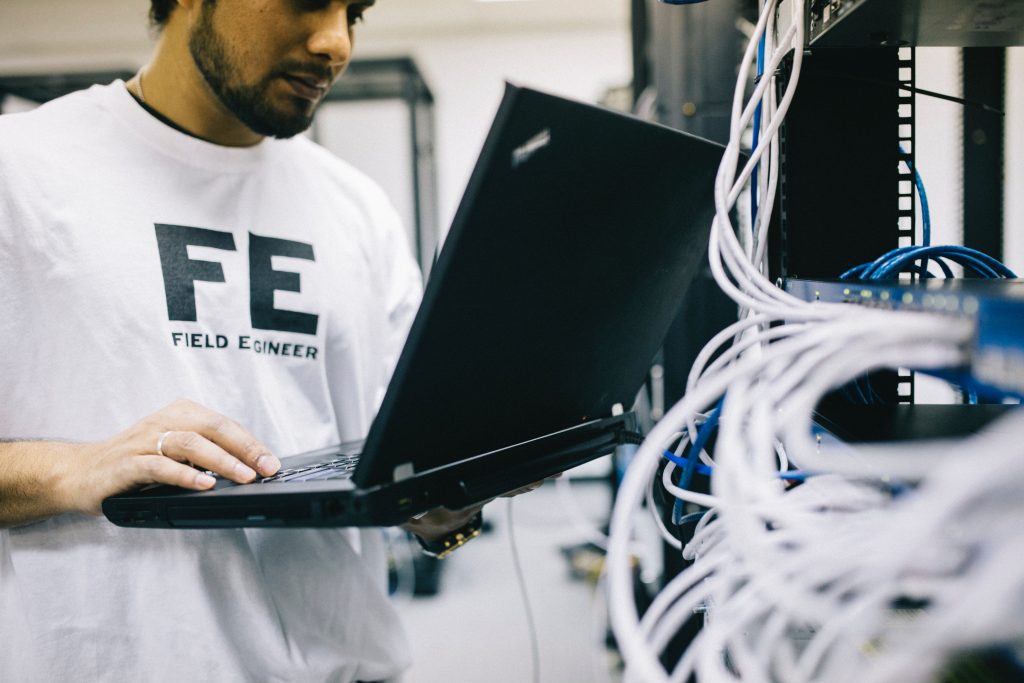
Read also: Demystifying RFID Technology: A Complete Guide
Training employees who will use the system is an important next step. Make sure they understand how to properly use the platform to record and access data efficiently. In addition, ensure good integration between this system and other existing systems in the company, such as asset management systems or safety reporting systems.
Real-time Monitoring and Data Analysis
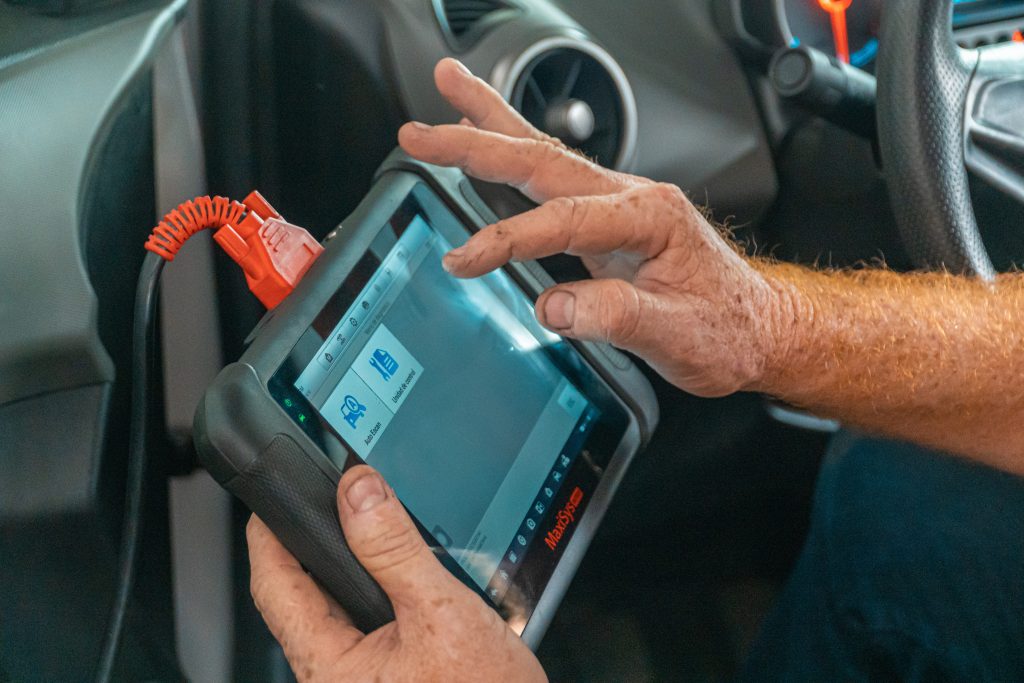
Read also: Operational Efficiency: Implementation of Digital Logsheet
One of the advantages of this system is the ability to carry out real-time monitoring of safety equipment. With information obtained directly, companies can respond to problems or potential risks more quickly. Additionally, in-depth analysis of the collected data will provide valuable insights to improve safety efficiency and reliability.
Benefits and Positive Impact of Implementing Digital Logsheets
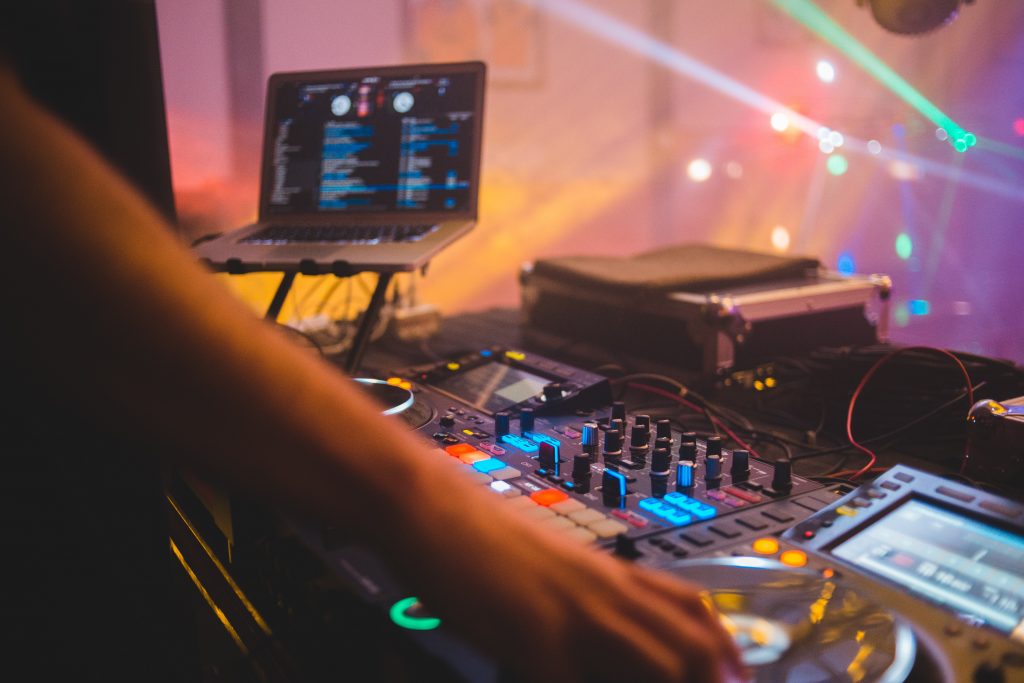
Read also: Data Security in Digital Logsheets: Challenges and Strategies
Implementation of this system brings various positive benefits. More efficient monitoring, quick response to potential risks, and the ability to track equipment safety history are some of them. With data recorded accurately and structured, companies can also better meet safety regulatory requirements.
Conclusion
Applying digital logsheets to safety equipment is a smart move that can increase safety efficiency and reliability in the work environment. With the right steps, companies can optimize safety monitoring, tracking and reporting more effectively. In this technological era, this system has become a tool that not only improves safety, but also productivity and overall work quality.
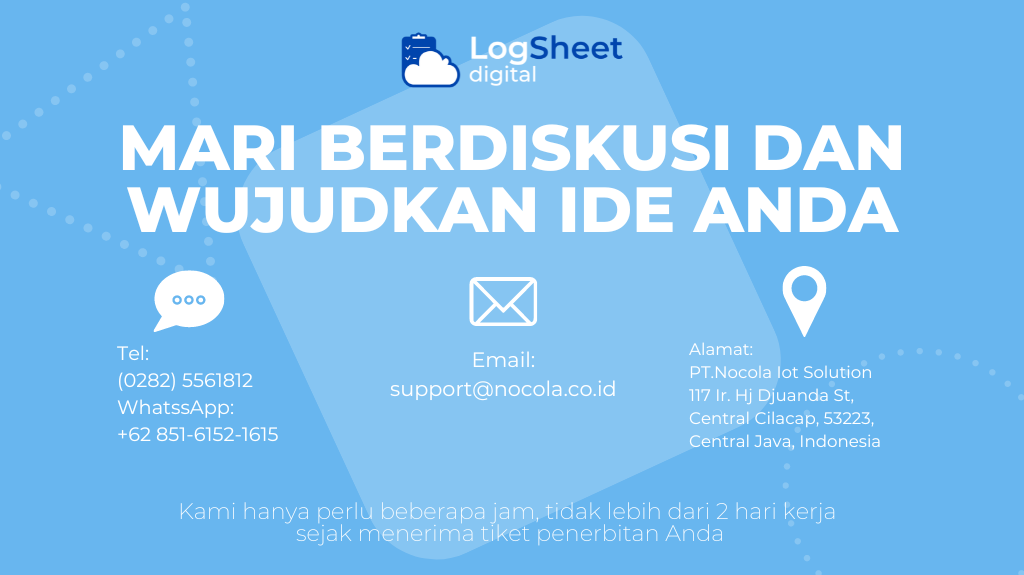
comments (0)