In the rapidly evolving industrial world, quality control is a key factor that determines a company’s success. This process requires accurate and structured documentation to ensure that every production stage meets the established standards. In today’s digital era, many companies are transitioning from manual logsheets to digital logsheets to enhance efficiency and accuracy in quality control. This article will discuss successful steps in implementing digital logsheets in quality control.
What Is a Digital Logsheets?
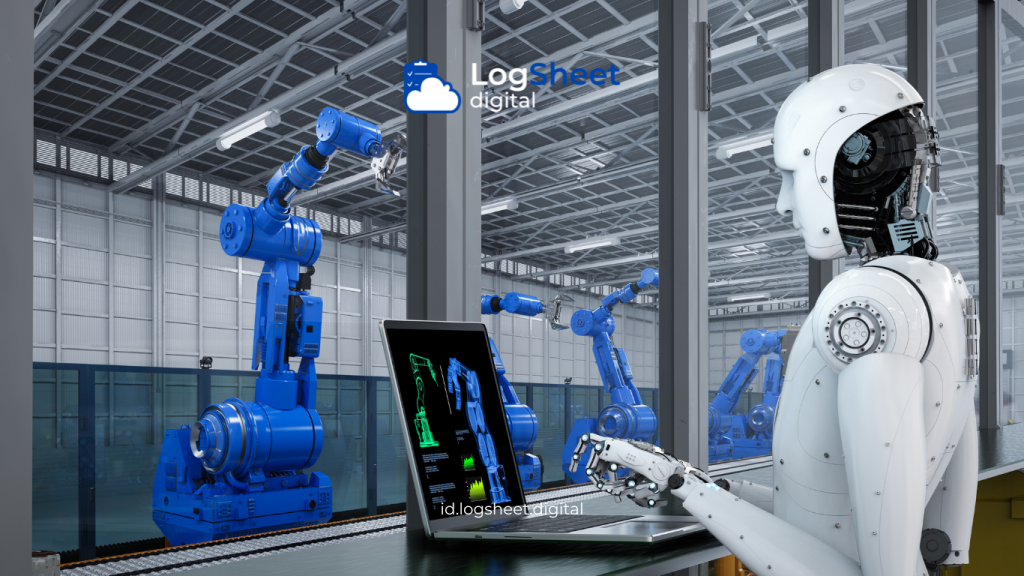
Read More: Advancing Towards Industry 4.0: Transformation with Digital Logsheets in Production
A digital logsheets is an application or software used to record and monitor production data in real-time. With digital logsheets, companies can store data electronically, facilitate access, and improve accuracy compared to manual methods. Digital logsheets also allow integration with other systems, such as ERP (Enterprise Resource Planning) or SCM (Supply Chain Management), to accelerate decision-making processes.
Benefits of Digital Logsheets in Quality Control
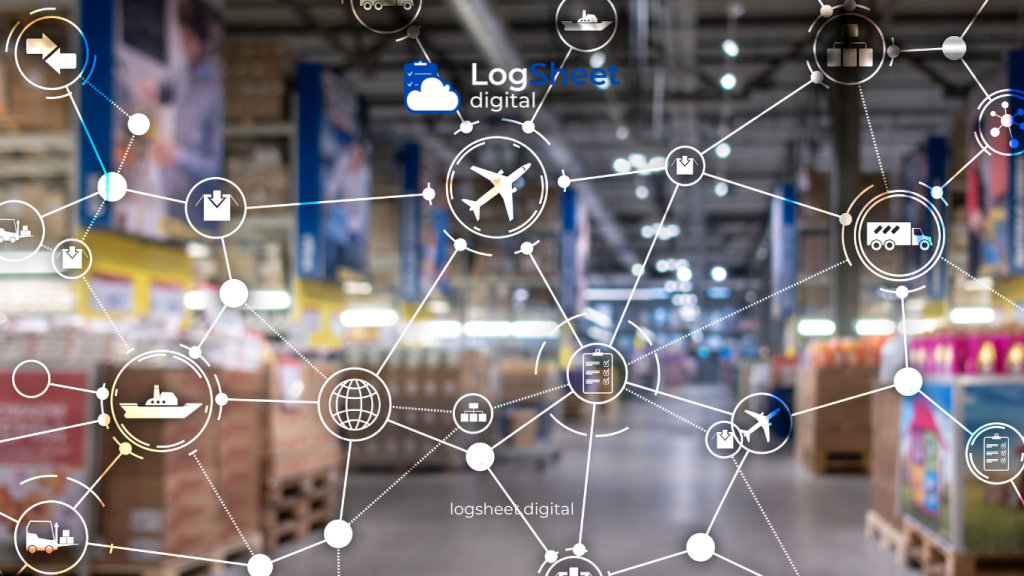
Read More: Smart Solutions: Digital Logsheets for Operational Health
The use of digital logsheets offers various benefits, especially in quality control. Some of them include:
- Data Accuracy: Reduces human error in recording and calculating data.
- Real-time Monitoring: Allows real-time quality monitoring without waiting for manual reports.
- Time Efficiency: Saves time required for recording and reporting.
- Easy Access: Data can be accessed anytime and anywhere, facilitating team collaboration.
- Data Security: Data is more secure as it is stored in a well-protected system.
Steps to Implement Digital Logsheets in Quality Control

Read More: Efficiency in Accident Reporting: Digital Logsheets in Safety Equipment
1. Identify Company Needs
The first step in implementing digital logsheets is to identify the specific needs of the company. This includes understanding the current quality control processes, determining the types of data that need to be recorded, and assessing the capabilities of existing systems. Through this identification, companies can determine what features are necessary in the digital logsheets to be used.
Analyze Quality Control Processes
Conduct a thorough analysis of the existing quality control processes. Identify critical points where manual recording might lead to errors or delays. Discuss with the quality team to understand the challenges they face and how digital logsheets can help address them.
2. Choose the Right Software
After identifying needs, the next step is to select the appropriate digital logsheets software. There are various options available in the market, ranging from customizable solutions to off-the-shelf ones. Consider features such as ease of use, integration with other systems, reporting capabilities, and technical support.
Evaluate Vendors and Service Providers
Before deciding on the software to use, evaluate the vendors or service providers. Ensure they have a good reputation, provide adequate technical support, and have experience in implementation in similar industries.
3. Plan a Phased Implementation
Implementing digital logsheets should be planned in phases to minimize disruptions to daily operations. Start with a pilot project in one department or area, then evaluate the results before expanding to the entire company.
Training and Preparing the Team
Before the system is implemented, conduct training for the team that will use the digital logsheets. Ensure they understand how the system works, the expected benefits, and how to address any issues that may arise. Proper preparation will ensure a smooth transition.
4. Integrate with Other Systems
To maximize the benefits of digital logsheets, integrate the system with other software already used in the company, such as ERP or SCM. This integration will allow data to flow seamlessly between systems, improving efficiency and accuracy.
Addressing Integration Challenges
Integration challenges may arise, especially if existing systems use different technologies. Work with IT teams or software vendors to ensure integration proceeds smoothly and meets the company’s needs.
5. Monitor and Evaluate
After digital logsheets are implemented, perform regular monitoring and evaluation. Track whether the system is operating as planned, if there are improvements in quality control, and if there are any issues that need to be addressed.
Feedback from Users
Collect feedback from system users to determine if they encounter difficulties or find ways to further enhance efficiency. This feedback is crucial for making adjustments and improvements to the system.
6. Continuously Improve
Quality control is an evolving process, and so is the digital logsheets system. Based on the evaluations conducted, make continuous improvements to the system to ensure that digital logsheets always meet quality control needs.
System Updates and Ongoing Training
Regularly update the system to keep up with technological advancements and business needs. Additionally, it is crucial to provide ongoing training to ensure that all users remain up-to-date with the latest features and functions of the digital logsheets system. By doing so, you not only keep the team informed but also enhance their ability to utilize the system effectively. Consequently, this approach helps maintain high levels of proficiency and maximizes the benefits of the digital logsheets over time.
Challenges in Implementing Digital Logsheets

Read More: Digital Logsheets: Development of Logistics Services and Enhancing Competitive Advantage
1. Resistance to Change
One of the biggest challenges in implementing digital logsheets is resistance from employees who are accustomed to manual systems. It is important to involve them in the planning and training process to reduce this resistance.
2. Implementation Costs
The cost of implementing digital logsheets can indeed be a barrier, especially for small companies. Nevertheless, this initial investment is frequently outweighed by the long-term benefits. In particular, the gains in efficiency and accuracy often justify the expense. Consequently, while the upfront cost may seem daunting, the enduring advantages in operational effectiveness and data precision make it a worthwhile endeavor.
3. Integration with Legacy Systems
Integrating digital logsheets with legacy systems often presents technical issues. Companies need to plan the integration carefully and may need to make adjustments to existing systems.
4. Data Security
Data security is a major concern, especially if digital logsheets are accessed via the internet. Companies need to ensure that the system is equipped with adequate security features to protect data from cyber threats.
Conclusion

Read More: Advantages of Operational Management in Digital Logsheets
Implementing digital logsheets in quality control is a strategic step that can bring many benefits to companies, from improved data accuracy to operational efficiency.
With digital transformation becoming increasingly important in the industry, the adoption of digital logsheets will help companies remain competitive and meet increasingly stringent quality standards. As a result, companies will not only improve internal efficiency but also, consequently, strengthen their position in a competitive market.
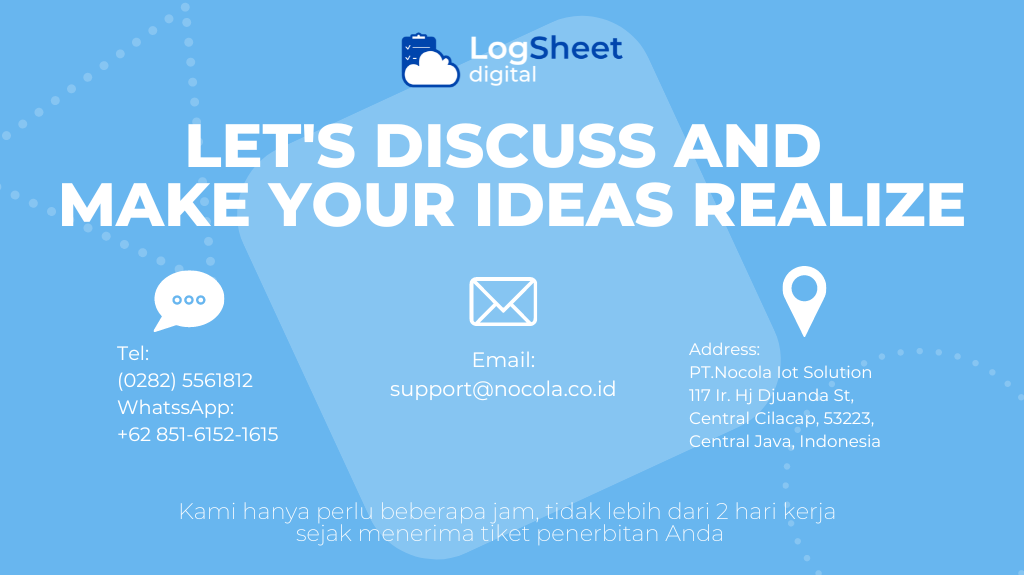
leave your comments