Revolution 4.0, or more commonly known as Industry 4.0, brings significant changes to the world of industry and manufacturing. Digital technologies, such as the Internet of Things (IoT), artificial intelligence (AI), and big data, have become the main pillars in creating more efficient, integrated, and autonomous production systems. One crucial element in this transformation is the use of digital logs, which replace traditional manual record-keeping and bring significant benefits in data management.
This article will discuss how digital logs play a role in supporting progress towards Industry 4.0, including the benefits gained, challenges faced, and steps that can be taken to optimize the use of this technology in the production process.
What is Industry 4.0?

Read more: Enhancing Production Transparency with Digital Logs: The Food Industry Case
Industry 4.0 is a concept that combines advanced technologies with traditional production systems to create more flexible, efficient, and productive “smart factories”. This concept includes process automation, data integration, and the use of digital technologies to improve production quality and speed. Industry 4.0 also encourages the use of technologies that enable machine-to-machine communication, real-time data analysis, and faster, more accurate decision-making.
Digital Logs: Definition and Function
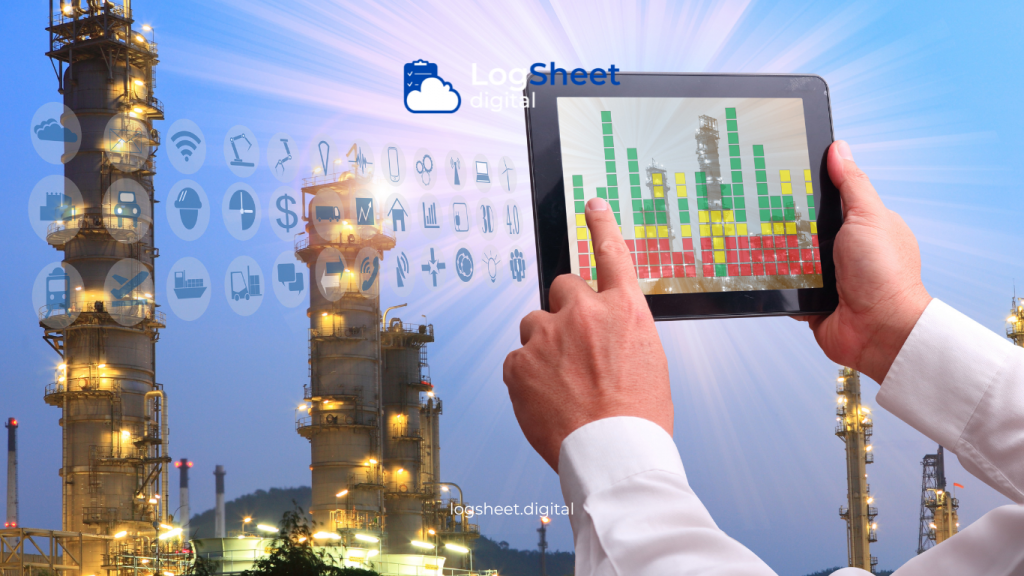
Read more: The Benefits of Digital Logs for Long-Term Performance Analysis
Digital logs are data recording systems that use digital software and hardware to replace manual recording methods. This system allows for the automatic and real-time collection, storage, and analysis of data, which is crucial in the context of Industry 4.0. Digital logs can include various information such as production time, the number of items produced, machine parameters, and working conditions.
The main functions of digital logs include:
- Accurate Data Recording: Digital logs reduce the risk of human error in data recording.
- Real-Time Production Monitoring: Automatically recorded data allows for real-time monitoring of production, facilitating quick decision-making.
- Data Analysis: Digital logs enable more in-depth data analysis to improve production efficiency and quality.
- Data Storage and Archiving: Digitally stored data is easier to access and archive for auditing and reporting purposes.
Benefits of Digital Logs in Industry
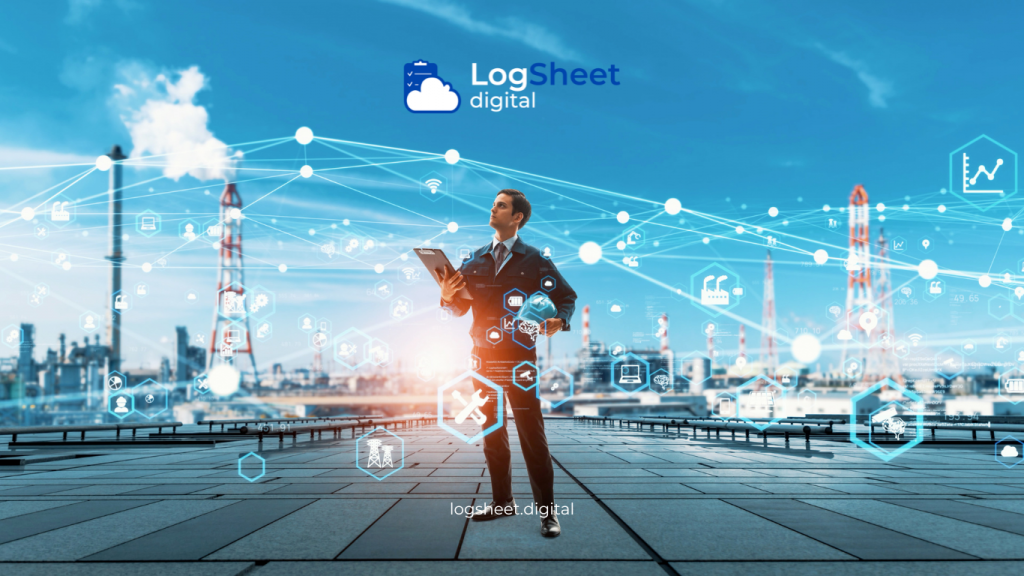
Read more: Digital Transformation in Safety Equipment Monitoring: The Role of Digital Logs
Higher Efficiency and Productivity
Using digital logs significantly enhances operational efficiency in factories. Automatically and real-time recorded data reduces the need for manual intervention, thus reducing downtime and increasing productivity. Additionally, this system allows for better time management by identifying and addressing bottlenecks in the production process.
Improved Product Quality
With digital logs, companies can monitor and control production parameters more strictly, ensuring that every product meets established quality standards. Recorded data can be used for more in-depth analysis, helping identify patterns that could cause product defects and allowing for immediate corrections before issues escalate.
Reduction in Operational Costs
Although the initial investment in digital log technology may be high, its long-term benefits are significant. Reduced human errors, higher efficiency, and improved product quality all contribute to overall reductions in operational costs. Additionally, digital logs help optimize resource use, reduce waste, and maximize output.
Compliance with Regulations
Digital logs make it easier for companies to comply with increasingly stringent industry regulations. Automatically recorded and well-stored data simplifies the auditing and reporting process. This system also allows for better tracking of each production stage, which is crucial in highly regulated industries such as pharmaceuticals and food.
Better Data Security
With digital logs, production data is stored digitally and protected with various security layers, such as encryption and role-based access. This reduces the risk of data loss and unauthorized access, ensuring that important information remains secure and available when needed.
Integration with Other Systems
Digital logs can be easily integrated with other systems used in factories, such as production management systems, quality control systems, and human resource management systems. This integration creates a seamless data flow across the organization, enabling more efficient monitoring and management of production processes.
Challenges in Implementing Digital Logs

Read more: Digital Logs for Equipment Safety Data Monitoring
- Implementation Costs
One of the main challenges in adopting digital logs is the initial high cost, including hardware, software, and employee training. Although the long-term benefits are significant, these upfront costs can be a barrier for companies, especially small and medium-sized enterprises. - Knowledge and Skills Gaps
Transitioning from manual to digital systems requires upgrading employees’ skills and knowledge. Employees accustomed to manual recording may struggle to adapt to new technology. Therefore, adequate training and education are crucial for successful implementation. - Cybersecurity
Although digital logs offer better data security, cybersecurity risks remain a major concern. Digital systems are vulnerable to cyberattacks, such as hacking and malware. Companies must ensure they have strong security measures to protect their production data. - Resistance to Change
Like other digital transformations, resistance from employees and management can be a challenge. Many people may be reluctant to adopt new technology due to uncertainty or fear of its impact on their jobs. Addressing this requires clear communication of the benefits of digital logs and involving employees in the transformation process. - System Interoperability
In an Industry 4.0 environment, interoperability between various digital systems is key to success. Challenges arise when different systems cannot communicate effectively with each other, hindering data flow and reducing efficiency. Ensuring that digital logs can integrate smoothly into the existing digital ecosystem is a crucial step in implementation.
Steps to Optimize the Use of Digital Logs
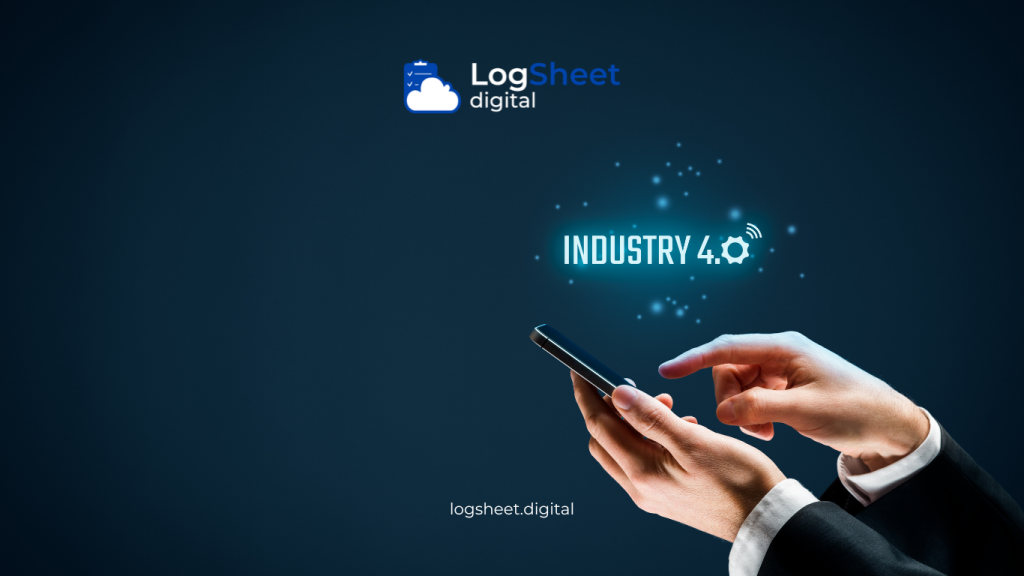
Read more: Optimizing Warehouse and Logistics Efficiency with Digital Logs
- Choosing the Right Platform
Selecting a digital log platform that meets the specific needs of the factory is an important first step. The platform should be user-friendly, scalable, and compatible with existing systems in the factory. Additionally, ensure that the platform provider offers adequate technical support to facilitate the transition from manual to digital systems. - Employee Training
Investing in employee training is key to ensuring the successful implementation of digital logs. Training should cover not only how to use the system but also an understanding of the benefits of this technology and how it can improve their work. Ongoing training is also important to keep employees competent in using technology as systems evolve. - System Testing and Adjustment
Before full deployment, it is essential to test the digital log system to identify and address any issues. Testing should cover all aspects of the system, from data recording to analysis and reporting. After implementation, the system should be continuously monitored and adjusted as needed to ensure optimal performance. - Integration with Existing Systems
To maximize the benefits of digital logs, integration with other systems in the factory should be carried out. This includes production management systems, quality control systems, and human resource management systems. This integration will create a smooth data flow across the organization, enabling better and faster decision-making. - Ongoing Monitoring and Evaluation
After implementation, it is important to continually monitor the performance of digital logs and evaluate their impact on the production process. Collected data can be used to identify areas for improvement and make data-driven decisions for further development. Periodic evaluations also help ensure that the system remains relevant and effective as technology and business needs evolve.
Conclusion

Read more: Digital Logs as a Monitoring Tool for Warehouse and Logistics Operations
The transformation towards Industry 4.0 by adopting digital logs in production offers numerous benefits, including improved efficiency, productivity, product quality, and data security. While challenges such as implementation costs, resistance to change, and cybersecurity need addressing, the right strategies can make digital logs a highly effective tool for supporting the advancement toward smart factories.
With the right platform selection, adequate employee training, and good integration with other systems, digital logs can significantly enhance production processes and contribute to achieving the goals of Industry 4.0.

comments (0)